The whole new yarn about sustainable fashion
-
- from Shaastra :: vol 03 issue 10 :: Nov 2024
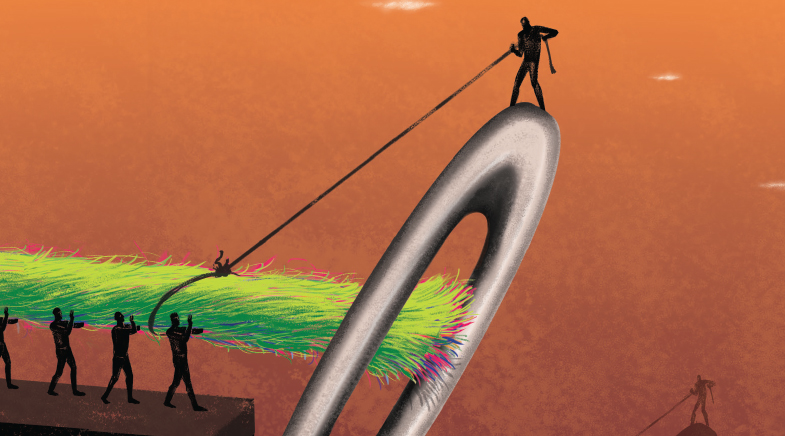
Scientists and start-ups are going the whole nine yards to fashion sustainable fabrics using alternative raw materials and new technologies.
Having grown up in India's polyester capital Surat, in a family with business interests in the popular clothing material, Shreyans Kokra was shocked to learn about the environmental impact of this synthetic fabric. It was the year 2016, and Kokra was doing his Master's in entrepreneurship at the Babson College in Massachusetts in the U.S. Keen to make a meaningful impact in the textile industry, he zeroed in on cotton as a prospective field of work, only to find that it came from a thirsty crop that used up large swathes of land and tonnes of fertilisers and pesticides that caused water pollution. His search for sustainable alternatives to polyester led him to 19th-century literature, which documented the use of agricultural waste to make fabrics. Hemp and nettle were used to make fabrics till the 20th century but were overshadowed by cotton, polyester and other cheaper alternatives.
Like all synthetic materials derived from petroleum, polyester does not decompose. On the contrary, it sheds fibre with each wash, contaminating water bodies and the food chain. According to the non-profit Ellen MacArthur Foundation, which is committed to creating a circular economy, 22 million tonnes of waste will enter the oceans from the textile industry from 2015 to 2050 (bit.ly/ocean-wastes). While this has an enormous impact on oceans, it also presents a $500 billion opportunity every year for the $1.7 trillion textile industry to recycle and reuse clothing material. Kokra and other entrepreneurs are, however, looking at a true redesign of the industry by developing alternative raw materials. "There is rising consumer pressure and also regulatory pressure," says Kokra, "not in India but in Europe."
In 2017, Kokra started Canvaloop Fibre in Surat to manufacture fabrics from agricultural waste. The existing process to make such fabrics was laborious and in need of new technology. The company first developed machines that could separate the fibrous portion from the agro-waste 100 times faster than traditional machines. The fibrous portion was then put through a biochemical process that removed everything in the waste except cellulose, lignin and pectin. An enzymatic treatment followed by a series of mechanical processes created fibres that matched the properties of cotton. The resulting material could be spun on cotton spinning machines to form a yarn, which could be woven or knitted to make any garment or apparel.
The company's fabric costs twice as much as cotton, but its prices are expected to drop with increasing scale, just as the input costs of cotton are supposed to rise over the decade. Canvaloop supplies fibres for blending with regular fibres such as cotton, linen or polyester to textile companies Arvind, Jayashree Textiles and others. This method is actually no more than an early experiment. There is not enough agricultural waste in the world to supply the entire industry with raw materials. Scientists are looking at other methods of making sustainable fabrics.
Rathinamoorthy R., an Associate Professor at the Vellore Institute of Technology, in Chennai, had worked on understanding textile pollution before he set his eyes on developing alternatives to polyester. Specifically, he started researching bacterial cellulose, a versatile material produced by bacteria and used in food, medicine, and paper. Rathinamoorthy aimed to use bacterial cellulose to develop fabrics, but initially wanted to create it in the lab using fungi rather than bacteria. The process requires growing selected fungal strains in a nutrient-rich substrate and allowing them to form a mat-like structure. This mat is later separated from the substrate, cleaned, dried, shaped to improve its properties and then dyed.
Bacteria and fungi produce cellulose that is free from impurities such as lignin and hemicellulose, and, hence, require less processing. This method does not use up large land resources either. Rathinamoorthy switched to bacteria from fungi for improved scalability. "Alternative materials like these cannot completely replace cotton or the environmental issues that exist in the market," he says. "But it will help to improve or reduce the ways to improve the circularity of the design."
While Rathinamoorthy's fabric is still in the R&D stage, bio-based fabrics are already making their way into the market. In Alappuzha, Kerala, Malai Biomaterials creates leather-like materials from bacterial cellulose grown on coconut water waste. Kanpur-based Phool makes a vegan leather alternative called Fleather from discarded temple flowers. Kolkata-based Atma Leather has developed leather from banana peels. Elsewhere, the Swedish company Mycorena (now part of Naplasol) is exploring the production of lab-grown leather using fungus. Boston-based start-up GALY has developed ways to grow cotton in the lab using cell culture.
In the last decade, many clothing brands have pledged to reduce their carbon emissions and have set targets to achieve them. Nike aims to reduce its carbon footprint by 63% by 2030 and reach net zero by 2050. Zara seeks to achieve net-zero emissions by 2040. Levi Strauss & Co. plans to reduce emissions in its owned-and-operated facilities by 90%, shift to 100% renewable electricity in those facilities, and reduce emissions by 40% across their entire supply chain by 2025. Roadmaps for the industry, being drafted around the world to achieve net-zero emissions, are expected to drive regulations that will force companies to disclose the mix of materials in their products. "So, they want to be prepared for that. That's what is pushing them on the regulatory side," says Kokra.
PAST ISSUES - Free to Read
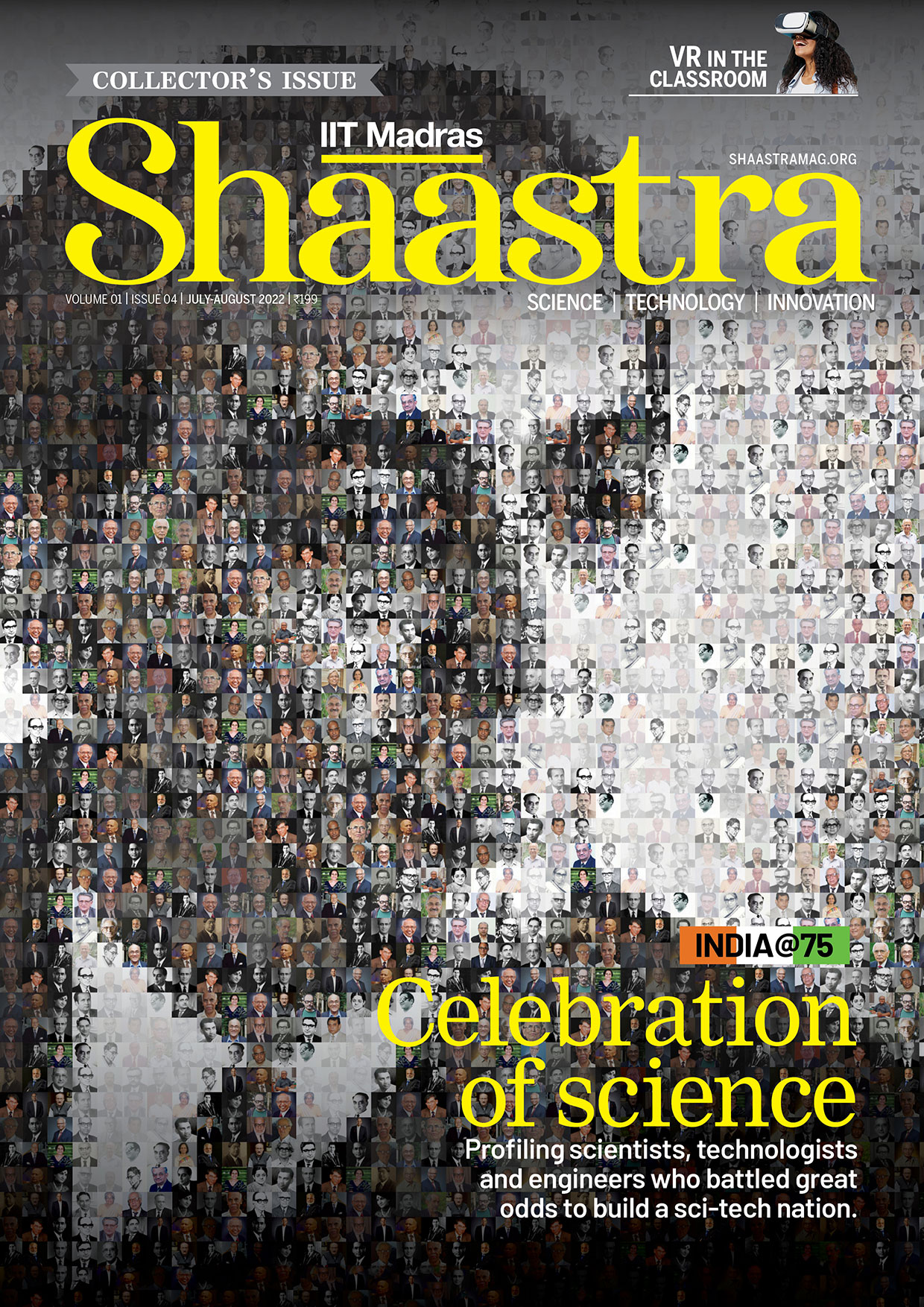
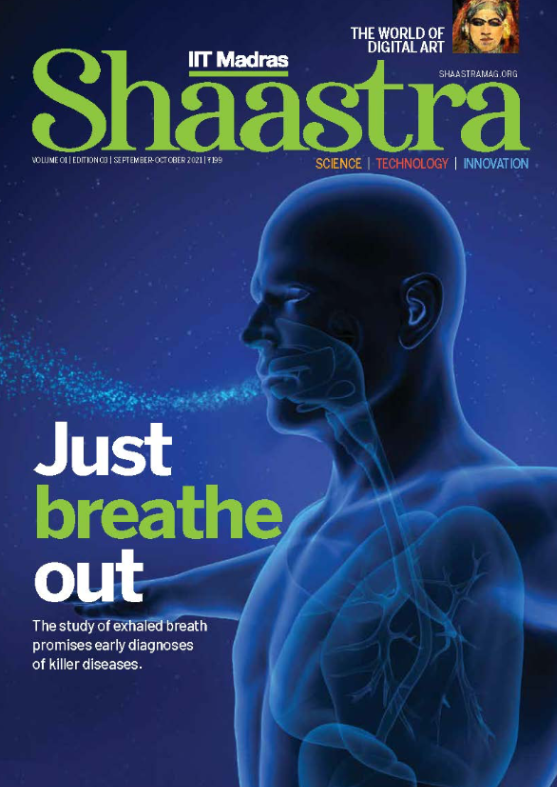
Have a
story idea?
Tell us.
Do you have a recent research paper or an idea for a science/technology-themed article that you'd like to tell us about?
GET IN TOUCH