All tanked up
-
- from Shaastra :: vol 03 issue 02 :: Mar 2024
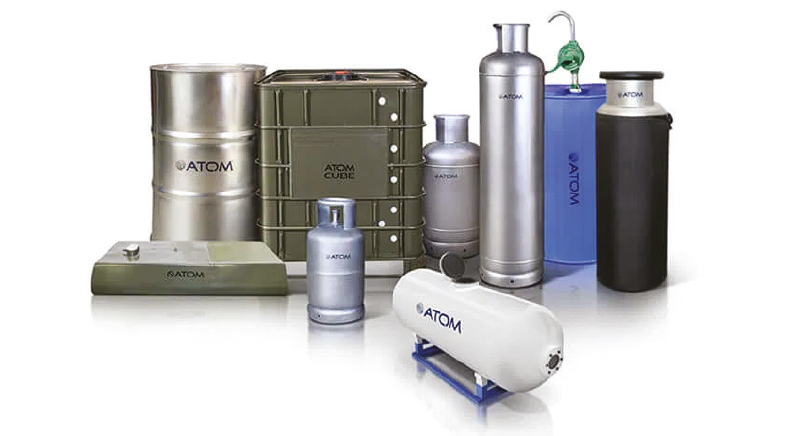
A start-up is developing world-beating technology for the safe transport and storage of hydrogen.
In October 2023, ATOM Alloys approached the Indian Institute of Science (IISc), Bengaluru, for help in solving a science problem of explosive proportions. Specifically, the firm signed an agreement with IISc's translational arm, the Society for Innovation and Development (SID), on a system for the safe storage of hydrogen.
Hydrogen is considered the fuel of the future as it is carbon-neutral. But it is so light that it can escape even air-tight vessels, endangering transport and storage. With countries across the world seeking to replace fossil fuels with hydrogen, there is an urgent need to create fail-proof systems for storing and transporting hydrogen.
Incorporated in 2016 under the government's Startup India initiative by its three founders – relatives Anil Nair, Ajit Tharoor, and Vinod Menon – ATOM Alloys has been developing innovative technologies to make the transport and storage of fuel safe at all levels – from huge tankers to fuel tanks in vehicles.
The company, which has developed a robust technology for fossil fuels, is now setting its sights on hydrogen storage. Company CEO Ajit Tharoor reckons that hydrogen represents the future even more than electric vehicles (EVs) do. The agreement with SID (at IISc), he hoped, would help the company develop its patent portfolio further to make explosion-resistant hydrogen fuel tanks.
With countries seeking to replace fossil fuels with hydrogen, there is an urgent need for fail-proof systems that store and transport hydrogen.
Unlike other fuel storage systems, a hydrogen tank can explode even in the absence of fire, sparked by just a leak from the tank. It interacts with oxygen in the air, causing an explosion. Besides, it can embrittle most materials commercially used for fuel storage and transportation, rendering them unsafe.
DEALING WITH BLASTS
The idea to develop an explosion-resistant technology stemmed from the founders' experience in West Asia's oil and gas industry, where they witnessed recurring explosions. "While some of these were accidents, others were attempted arsons, which frequently occur in strife-torn areas," Tharoor says.
In the early 2010s, the team got an opportunity to develop some explosion-resistant fuel tank prototypes for buses that carried security personnel in Jammu & Kashmir as well as for bullet-proof vehicles used by the Special Protection Group in India. "The vehicles they were using were bullet-proof, but their fuel tanks were not protected. If anything happened to the fuel tank, the whole vehicle could explode," Vinod Menon, the company's Chief Technology Officer, adds.
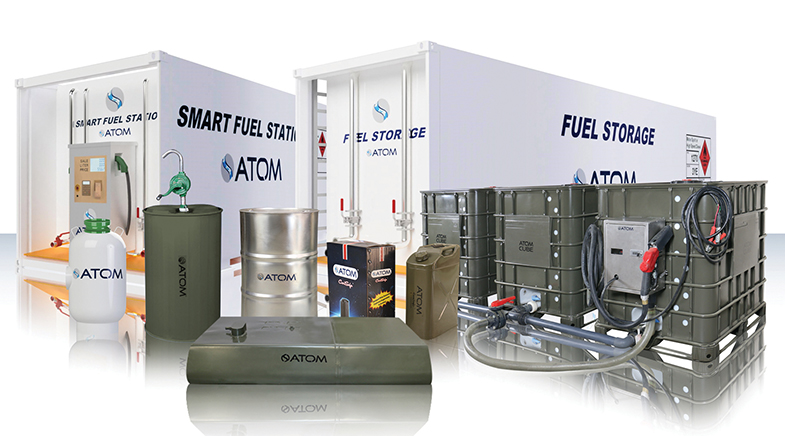
The team went on to perfect its fledgling explosion-resistant technology and got it evaluated by the Southwest Research Institute in Texas, the Illinois-based Underwriters Laboratories, a global safety science company, and other certifying agencies.
In any fuel tank, Menon explains, there is liquid fuel and vapour. The vapour, a mix of fuel fumes and air, is extremely volatile. "When a fire or for that matter superheat or pressure from an explosion outside is introduced, the vapour inside the tank gets ignited. The large column of vapour inside results in rapid combustion, which can lead to an explosion when the flame speed attains supersonic velocities," he says.
SAFETY LAMP SHOWS THE WAY
The company's proprietary technology is modelled loosely on the principle that British chemist and inventor Sir Humphry Davy used in 1815 to invent a safety lamp. The lamp, used in hazardous mining operations, is a wick lamp with the flame enclosed in a mesh screen. While the screen allows the air to come in to sustain combustion, the holes in the mesh are too fine to allow a flame to propagate through them and cause an explosion.
Hydrocarbon fuels have a maximum flame speed of 30-40 centimetres per second in laminar flow (when there are no disturbances). In the case of hydrogen, the speed is 1-1.5 metres per second. But if the situation is turbulent, the flame amplifies ten times, says Amit Kumar, Professor of Aerospace Engineering at the Indian Institute of Technology Madras. In confined spaces, the velocity of the flames during turbulence will increase to reach detonation levels. "If the fuel is coming out of the container, but there is a restraint (like the Humphry Davy device), the flame will not go inside the container and burn happily outside," Kumar says.
The ATOM Alloys team, with development centres in Mumbai and Dubai, has the technology to protect fuel storage and transportation units. At the heart of the technology — Explosion Prevention System — is a reticulated alloy mesh, which has high thermal conductance and flame-quenching properties. "When heat is introduced to the mouth of a fuel tank and if the heat goes uncontrolled, it goes in. But the alloy we designed acts as a thermal conductor and dissipates the heat across the body of the tank. This prevents any hot points in the tank," Menon explains.
Since the whole area of the mesh is divided into small cells, fuel vapour gets trapped in these cells, resulting in controlled deflagration. Since the flame will move from cell to cell, it is possible to quench its movement. It will not attain supersonic velocity, which is a necessary condition for an explosion to take place, he says.
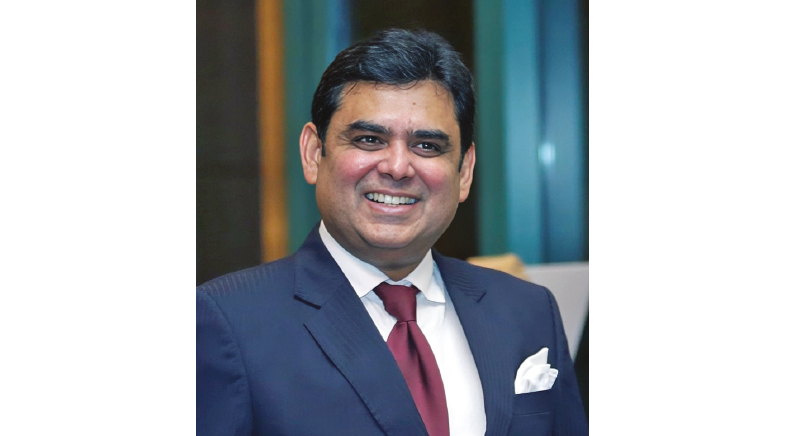
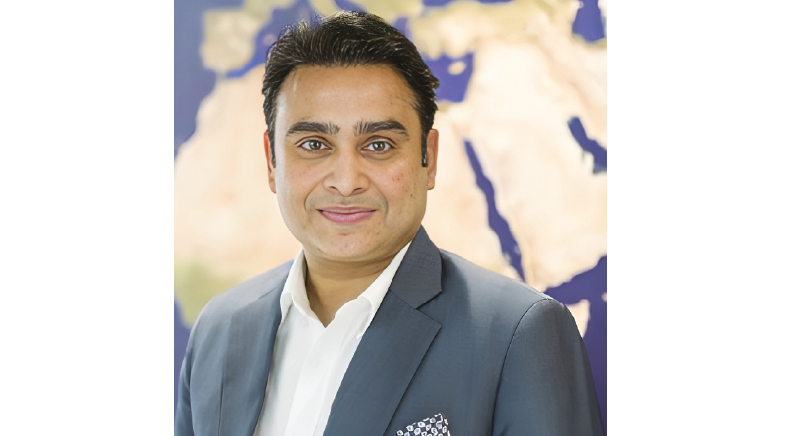
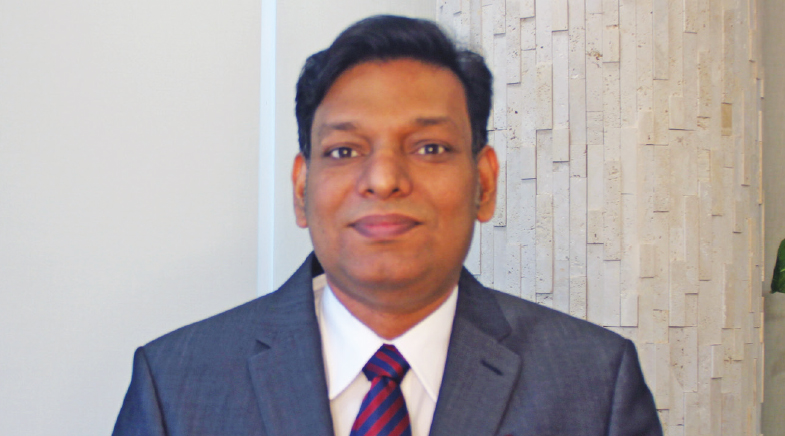
ATOM Alloys, founded by Anil Nair, Ajit Tharoor and Vinod Menon, has been developing innovative technologies for safeguarding fuel transport and storage.
MESH HINDERS HEAT FLOW
Another pillar of safety introduced by the team is the structured packing of the mesh inside the fuel container. In fuel tanks and wagons designed by the firm, this structured packing reduces the sloshing of the liquid and hinders the flow of heat and combustion energy through it. The mesh is so porous that it occupies only 1-3% volume of the container.
"The technology that they developed is very sophisticated... As of now, it is the only explosion-resistant technology approved for fuel storage and transport in the world," says Kamanio Chattopadhyay, Honorary Professor, Department of Materials Engineering, IISc. Chattopadhyay will work with the firm closely on the project.
The 'Atomised tanks', as they are called, are capable of storing and transporting any liquid or gaseous fuels, including biofuels. Co-founder Anil Nair says the tanks have been tested with all kinds of fossil fuels and found to be explosion-resistant.
The firm has been granted patents in Israel, the Gulf Cooperation Council (GCC) countries, Japan and the U.S.; patents are pending in India and 37 other countries. The firm has approvals and orders from companies in the U.S. and Japan. In India, ATOM Alloys has been working with Indian defence agencies to design new-generation fuel dumps for storage in frontier areas as well as fuel tanks for aerial vehicles. "In countries like Ukraine we have seen drones, which cost a few hundred dollars, being used to attack fuel storage tanks so that the entire area can be destroyed," Nair says.
The firm has been granted patents in Israel, GCC countries, Japan and the U.S.; patents are pending in India and 37 other countries.
Nair adds that the company has completed all aspects of commercialisation (of the technology) for hydrocarbon fuels: gasoline, gasoil, naphtha, kerosene, ATF, biofuels such as ethanol and LPG. "For ammonia, which is a preferred fuel nowadays, we have almost finished our work and we have to now get down to certification testing," he says.
CLOSER TO A SOLUTION
Chattopadhyay says that a class of explosion-resistant fuel tanks built by the company is similar to modern hydrogen tanks. This, he says, is expected to take it closer to a potential solution to the problem of storage.
There are, however, problems associated with hydrogen storage and transport. "Hydrogen is a small molecule that can move through the metal and occupy the defects in the metal. This leads to embrittlement over a period of time," explains Chattopadhyay. In nuclear fission plants, where hydrogen is produced during a nuclear reaction, this is managed by using zirconium alloys. But using these for hydrogen storage is not commercially feasible.
"We have to manage this problem using commercially available materials. That is the challenge," Chattopadhyay says.
Menon adds that the initial part of their study will be conducted with IISc. "We are taking the work ahead on other fronts and very confident that we will make an explosion-resistant hydrogen fuel tank sooner than later," he says.
Have a
story idea?
Tell us.
Do you have a recent research paper or an idea for a science/technology-themed article that you'd like to tell us about?
GET IN TOUCH