Insect farming takes wing
-
- from Shaastra :: vol 03 issue 07 :: Aug 2024
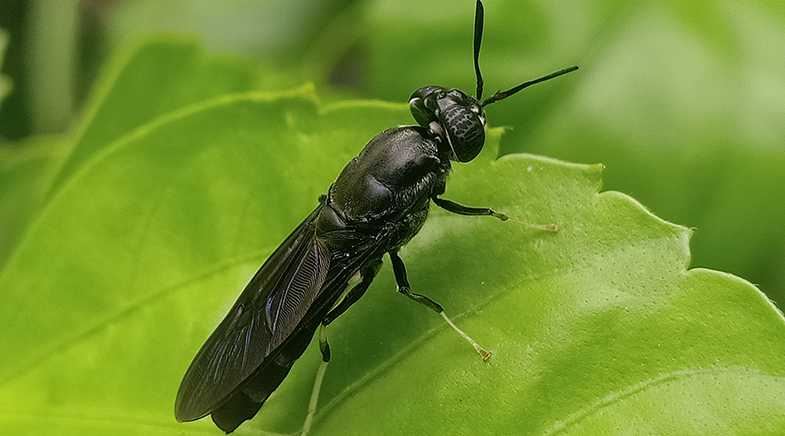
The flutter you hear is of farming insects, which are top-notch garbage cleaners and storehouses of proteins.
Arun Kumar Das was working on a waste management project several years ago when a friend told him about the wonders of Hermetia illucens, a wasp-like insect. Das, who specialises in establishing social sector development programmes, was too engrossed in his work to pay much heed to the insect, commonly known as the black soldier fly (BSF), because of its black, metallic wings. But a few years down the line, with time on his hands during the COVID-19-imposed lockdown, Das began to give some thought to the insect that had come so highly recommended. He has thought of little else ever since: you could say he's got a bee in his bonnet.
The fly, which originated from South America and is now found almost everywhere, is the buzzword in insect farming. In the 1990s, researchers discovered that its larvae could break down garbage more quickly and efficiently than other insects or microbes. Moreover, the engorged larvae are storehouses of protein, fatty acids, lipids, and vitamins, and can be effectively harvested for these products.
Enthused by the insect's many properties, Das put together a team to design a hybrid bioreactor for these larvae in Bhubaneswar, Odisha. The bioreactor runs on solar and conventional electricity and is equipped with sensors to detect changes in temperature, humidity, and gases such as carbon dioxide, ammonia, and methane. Connected to the Internet, it can be monitored and adjusted remotely. In October 2022, Das joined forces with Benjamin Rubin, an Israeli geneticist and an entrepreneur, to launch Insectika Biotech, with research units in India and Israel. They are in the process of designing an autonomous breeding bioreactor for BSF eggs.
WEALTH FROM WASTE
For BSF farming, organic garbage with newly hatched larvae is put into the bioreactor. Seven to ten days later, the trash is gone. In its place are loads of plump BSF larvae ready for harvest. These are dried and then defatted in a process similar to cold-pressing oil from seeds. Proteins are extracted from the remaining material. Four tonnes of garbage yield 300 kg of protein and 100 litres of oil. Proteins and oil are feed additives for poultry, farmed fish, and shrimp. The frass/excrement becomes farm fertilisers, though Das has plans to extract protein from it, too.
Insectika's pilot plant at the Central Institute of Freshwater Aquaculture processes four tonnes of segregated municipal waste every week.
"From the user perspective, this is exactly how simple we want it," Das says. The details behind the simplicity are intricate. While BSF is quite a cooperative insect, its output has to be maximised when used on an industrial scale. A change in temperature, humidity, or gas levels can make the grubs moody and cause them to stop feeding. While the insects thrive at 25-32°Celsius and a humidity of 80-85%, Insectika has worked out optimum environmental requirements through artificial intelligence and machine learning, and programmed its reactors accordingly. Since it targets a global market, these reactors are also undergoing testing in different environments — such as Italy, Finland, and Kenya.
Insectika is testing its protein and oil feeds at the government-run Central Institute of Brackishwater Aquaculture and in the poultry sector. It hopes to hit the market when its commercial reactors are ready. It currently has a pilot plant at the Central Institute of Freshwater Aquaculture, Bhubaneswar, where it processes four tonnes of segregated municipal waste every week. "On the one hand, we can tackle the garbage problem; on the other, we provide an environmentally sustainable feed, replacing soy, which is resource-intensive," says Das. Scaling up operations is the key: Bhubaneswar alone generates 700 tonnes of solid waste daily.
While people have used insect-derived products such as honey, silk, and lac for millennia, scientists and entrepreneurs have in recent years shown a deep interest in insect farming. Researchers seek solutions from insects to a host of present-day issues, such as tackling pollution or creating sustainable supply chains for proteins, lipids, chitosan, and other materials that insects naturally produce.
INSECTS SHOW THE WAY
The use of insects to remove harmful chemicals from a substrate is called entomoremediation. As saprophagous insects — those that feed on decaying matter — devour the contaminated substrate, heavy metal contaminants such as cadmium end up in the puparium, without impacting the growth of the insect. The metals can be extracted from the spent pupae. Many moth and other insect larvae (superworms, mealworms, and so on) have demonstrated the ability to devour plastic waste, though their use for large-scale remediation is still being studied (bit.ly/insect-plastic). Another entomoremediation method being researched is the genetic modification of fruit flies and other insects to enable them to digest industrial pollutants such as bisphenols. Most of these developments are, however, still in laboratories.
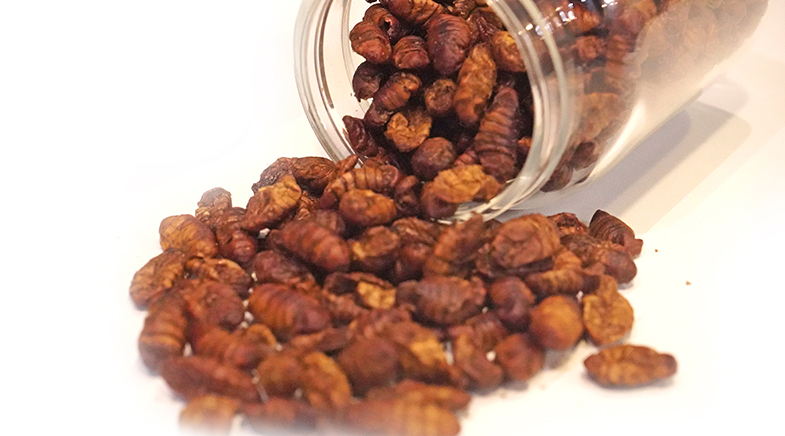
In Bengaluru, Ankit Bagaria and Abhi Gawri, graduates from the Indian Institute of Technology (IIT) Roorkee, founded Loopworm, a biosciences and biomanufacturing company that sees insects as not just a waste remedial solution, but as biofactories for the production of high-value products. While they, too, began with the BSF, a drive to Mysuru a couple of years ago became a game-changer. Passing through the silk-manufacturing town of Ramanagara, they were hit by the stench of rotting pupae and realised a ready source of insect protein was available there. They instituted a door-step collection system of used cocoons, and Bombyx mori — the silkworm — is now their primary insect source.
Loopworm sells a range of insect oils and protein mixes mainly for the farm feed sector and pet industry. It plans to launch high-value insect-derived molecules such as fibroin (used as a biomaterial, especially in wound healing), sericin (used in making cosmetics), and protein hydrolysates (used in cosmetics and as farm biostimulants). Loopworm's big plan, however, is to use insects as biofactories to produce proteins on demand.
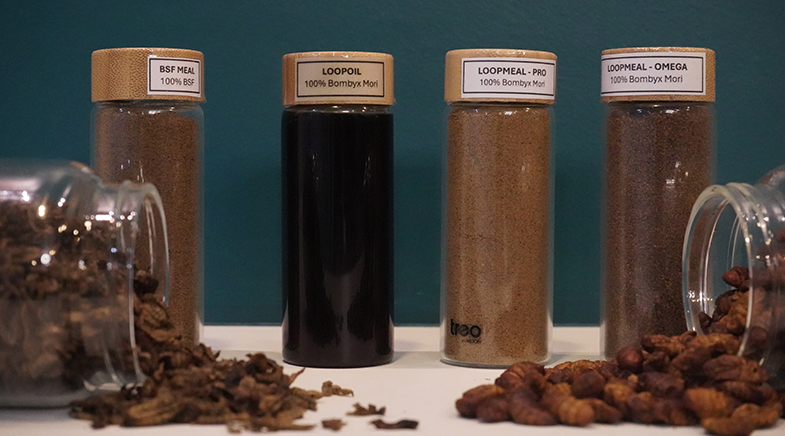
Loopworm, a biosciences and biomanufacturing company, sees insects as not just a waste remedial solution, but as biofactories for the production of high-value products.
An insect biofactory is a new area of scientific research. It usually involves infecting an insect with a baculovirus (insect virus) with a modified gene expression. The baculovirus takes over the machinery of the host insect to produce the desired protein, which is then harvested. For instance, one research details how to use the larvae of fall armyworm (an agricultural pest) to produce a recombinant version of the violin spider's venom (used for its antidote). Traditionally, extracting venom from spiders is a laborious task with a low yield. Through the insect biofactory method, the amount of venom from 17,000 spiders could be replaced with the work of 1,600 larvae (bit.ly/venom-antidote). While most of such research is still in laboratories, a Spain-based biotech enterprise, Algenex, is researching whether moth chrysalises could be used as living bioreactors for speedy and scaled-up vaccine production (bit.ly/chrysalis-vaccine).
At Loopworm's lab, research is being conducted on how the Bombyx mori can produce commercially valuable proteins such as Fibroblast Growth Factor (used in biocosmetics) and Foetal Bovine Serum (used in cell cultures). "We have developed a non-transgenic technique, for which we are in the process of applying for a patent," says Bagaria. Initial testing of the technology has already created fluorescent silkworm cocoons, so he is confident of the protein expression. "We have seen significant protein yields compared with using E. coli as biofactories for manufacturing proteins. However, there is still a lot of research (to be done) before we can create a product for the market," he says.

Close to Loopworm's unit is Fibroheal Woundcare. Started by entrepreneur Vivek Mishra, it produces a range of wound-healing products from silkworm protein. Fibroheal, too, uses discards of the silk industry (That's a wrap!).
ON THE MENU
Insects are a part of the traditional diet of many cultures, and an estimated 3,000 kinds of insects are eaten globally. In just the north-eastern region of India, there are several hundred edible species.
Insects make a nutrition-packed meal, as they are rich in proteins, lipids, unsaturated fatty acids, antimicrobial peptides, and vitamins. Their growth cycles are rapid, and they do not require large tracts of land or copious amounts of water to be farmed (see graphic). They convert low-protein feed into edible protein efficiently, and their small size results in low emissions of greenhouse gases and ammonia. It takes eight times more land to obtain one gram of edible protein from meat than from mealworms. Broiler chickens emit 32-167% more carbon dioxide than mealworms (bit.ly/eat-insect-nutrition).
Though efforts have been made in Europe and elsewhere to develop gourmet products such as cookies and pasta from insect proteins, these are niche attempts. That is because, apart from the general reluctance to eat insect products in many societies, extensive regulations are required for manufacturing edible products in this segment. In the West, human-grade insect protein is derived from insects fed on pre-production food waste (from factories) and not post-consumption waste.
But Prachurjya Dutta, a scientist at the Council of Scientific & Industrial Research-North East Institute of Science and Technology, Jorhat, believes people will accept insect-based food if it is marketed well. He points out that insect farming has evoked considerable interest since it has a very small carbon footprint. "Look at the number of research papers on insects as food, feed, and therapeutics," says Dutta, who has been studying the nutritional properties of edible insects in the region since 2015. "A decade ago, there were a dozen or so publications on these topics; today, there are over 150 a year," he says. Dutta has developed a protein hydrolysate from silkworm larvae for sports nutrition and hopes to transfer the technology for a marketable product.
At the lab that he shares with Senior Principal Scientist Jatin Kalita, the focus is on identifying the active biotic components in indigenous insects that can be of human value. These include identifying glucose-lowering compounds from the field cricket, antioxidant compounds from hornets, and anti-inflammatory compounds from silkworms. "We've seen these properties in cell cultures, and we are trying to identify the actual compounds," he says. Dutta is also trying to farm indigenous grasshoppers to see if they can replace BSF as an animal feed source. "The potential of insects is phenomenal," he says.
The potential hinges on scalability and acceptance, points out Bhanu Prasad, mentor for livelihood-generating, social impact start-ups. Having helped insect-based start-ups in Colombia, Malaysia, and India, he believes that insects are the alternative to plant-based products in the animal feed sector. "The challenges are not the science, but breaking into the market with standardisation, biohazard safety protocol, and scaled-up supplies," he says. The cosmetic and nutraceutical sectors hold promise, too, he says. Making inroads into the food market will be the biggest challenge, Prasad adds.
Have a
story idea?
Tell us.
Do you have a recent research paper or an idea for a science/technology-themed article that you'd like to tell us about?
GET IN TOUCH