These biofuels keep the engines revving
-
- from Shaastra :: vol 03 issue 06 :: Jul 2024
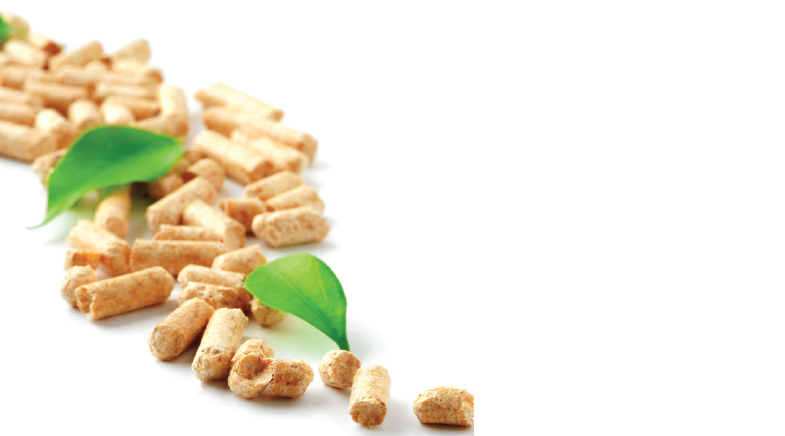
The focus is on turning agri-waste into biofuels — with robust supply chains and efficient technologies.
Kishan Karunakaran's interest in biofuels was sparked by former President A.P.J. Abdul Kalam's advocacy of renewable energy from agricultural residues. But when the mechanical engineer tried producing biofuel some 15 years ago, he encountered bottlenecks that limited growth and prevented him from making a profit. Over the years, he realised that the raw material needed to make biofuels was not easy to collect and transport, because of the seasonal variations and the geographically dispersed nature of agricultural residues and biowaste. To resolve the issue, Karunakaran, with friends Venkat Selvan and Sumanth Kumar Selvarasu, launched Buyofuel, a Coimbatore-based online platform connecting waste sellers, biofuel manufacturers, and fuel consumers.
The supplier side comprises sellers of used cooking oil, agri-waste, sawdust, plastic waste, rubber waste, and other such wastes. The manufacturers consist of plants — small or big — that use waste to make solid, liquid, or gaseous biofuel. The consumers are industries such as paper, steel, pharma, and power that can replace their petrol, diesel, and coal requirements with biofuels for plant operations. The start-up, founded in 2020, also has an on-field team that helps rural sellers perform online transactions on the platform.
The platform deals with wastes such as rice husks, wood chips, animal tallow, and sawdust. "Every type of end-of-life waste can theoretically be converted into fuel... So, we don't restrict our waste," says Buyofuel Chief Executive Officer Karunakaran, who has also done a Master's in Business Management.
President Kalam had suggested the cultivation of Jatropha curcas, an oil-rich seed, for the production of biodiesel. In 2008, Karunakaran started a venture to manufacture Jatropha biofuel, but the business did not prosper, and he shut it down in 2014. But since then, there has been a focused interest in the potential of biofuels in India. The government has ushered in policies to help those in the biofuel business. "Now there's a drive within companies to move towards net zero," Karunakaran says.
STRONG POLICY PUSH
Burdened by growing oil imports, the Indian government introduced its National Policy on Biofuels in 2018, to utilise, develop, and promote domestic feedstock for the production of biofuels. The policy emphasised setting up second-generation bio-refineries and promoted the development of new feedstock for biofuels as well as novel technologies for conversion to biofuels. It pushed the demand for ethanol and biodiesel by setting a target of 20% blending of ethanol in petrol and 5% blending of biodiesel in diesel by 2030. When India reached its 10% ethanol blending target five months ahead of its June 2022 goal, the government advanced the 20% ethanol target to 2025-26.
Achieving the 20% blending target would save India about $4 billion a year, but it would require an ethanol production capacity of 1,016 crore litres by 2025.
According to a 2023 report by the International Energy Agency (IEA) (bit.ly/iea-biofuel), India was the world's third-largest producer and consumer of ethanol in 2023. That year, India also initiated and launched the Global Biofuel Alliance, which seeks to serve as a catalytic platform, fostering global collaboration for the advancement and widespread adoption of biofuels. These measures also helped develop India's biofuel ecosystem, pushing scientists and entrepreneurs to come up with technologies that could efficiently convert waste to fuel.
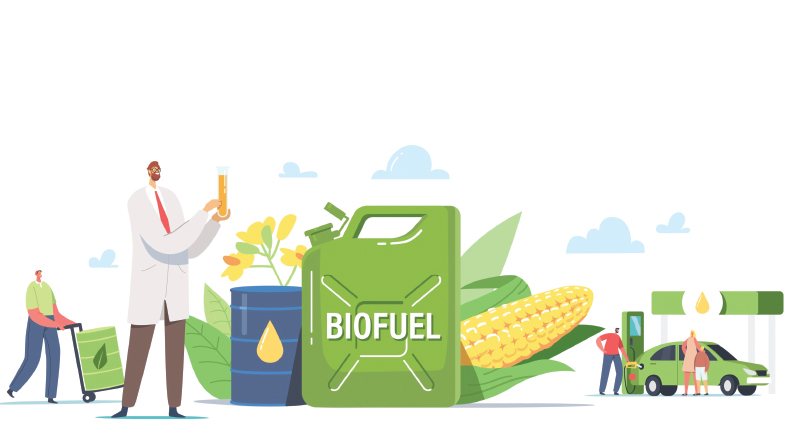
Achieving the 20% blending target would save India about $4 billion a year, but it would require an ethanol production capacity of 1,016 crore litres by 2025 (bit.ly/ethanol-target). While first-generation (1G) ethanol from food crops will put pressure on land and water resources, producing ethanol from biomass will be more sustainable and cut greenhouse gas emissions. With biomass becoming a raw material, farmers would rather cut and sell it than burn it — a practice that contributes to air pollution and soil degradation. According to a 2022 IEA report (bit.ly/feedstock-biofuels), India can annually produce 51.35 billion litres of bioethanol (2G ethanol) from 178 metric tonnes of surplus crop biomass. The report recommends adopting supply chain models — such as Amul's milk model and the National Dairy Development Board's fruit and vegetable model (Safal) to deal with biomass supply chain management. Amul and Safal have highly integrated supply chains that connect farmers to consumers, reducing intermediaries and thereby lowering costs and ensuring quality control. The report also highlights the urgent need to develop cost-effective pre-treatment technology and indigenous enzymes for ethanol production from biomass to make 2G ethanol cost-competitive compared to 1G ethanol.
ENZYMES AT WORK
Scientists and entrepreneurs are looking at breakthroughs as well as tweaking old methods to bring new results. Take the traditional practice of fermenting yeast in sugary juices to produce alcohol or ethanol. Producing ethanol from corn or rice, however, requires an additional step: enzymes are used to convert corn or rice into sugar, and this sugar is then fermented to yield ethanol. While producing ethanol from food crops is straightforward, using agri-waste as raw material is challenging.
Because of its complex structure, lignocellulose — or agri-waste — does not easily break down into sugar. Agri-waste needs to be pre-treated with chemicals. Enzymes are required to turn the broken lignocellulose into sugars, and ethanol is obtained through fermentation. The pre-treatment process and enzymes are key steps, but India lacked the facility for indigenous production of the enzymes.
"To convert cellulose to sugars, which is the most important digestive step, we are dependent on an imported enzyme. Each biofuel plant in India needs 5,000 tonnes of enzymes every year," points out biotech entrepreneur Subramani Ramachandrappa. It would be of little help if crude oil had to be replaced by expensive enzymes.
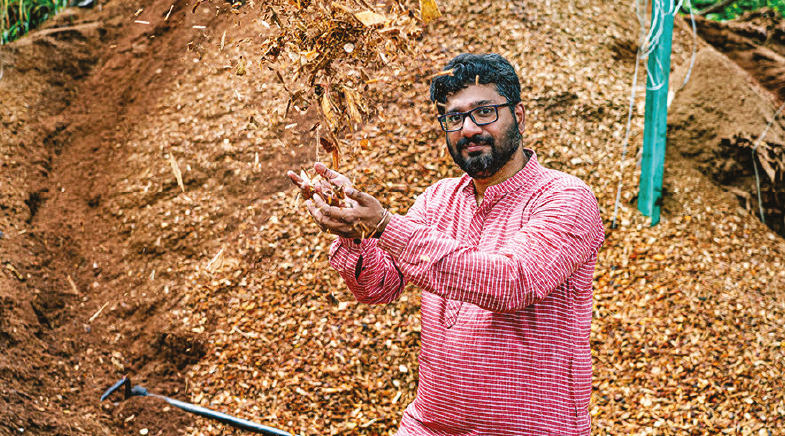
Ramachandrappa wanted to produce biomaterials from sugar and needed a powerful enzyme to do that. He realised that a fungus could help produce such enzymes. "Mushroom grows on paper or wood or straw or biomass. It's doing the same thing: it is releasing these enzymes, converting them into sugar, and absorbing it," says Ramachandrappa, who founded Fermbox Bio in Bengaluru in 2022 (For a better tomorrow).
The company partnered with Dyadic, based in Florida, in the U.S., and utilised the latter's proprietary Dapibus™ filamentous fungal-based microbial protein production platform. Using this platform, Fermbox Bio was able to tweak the fungus to produce the large quantities of enzymes required to produce sugar from agri-waste. Their enzyme cocktail consists of five enzymes that together break the complex agri-waste to produce cellulosic sugar. The cocktail is as effective as the enzyme cocktail from the Denmark-based Biotech company Novozymes and is cost-competitive. Ramachandrappa proposes to build an enzyme factory on the biofuel plant site to further bring down the enzyme costs by 30%.
With an investment of ₹14,000 crore, the Ministry of Petroleum and Natural Gas is helping public sector oil marketing companies set up 2G bio-refineries.
Enzymes and 2G bio-refineries are the focus of the government, too. With an investment of ₹14,000 crore, the Ministry of Petroleum and Natural Gas is helping public sector oil marketing companies such as the Indian Oil Corporation Limited (IOC), Hindustan Petroleum Corporation Limited (HPCL), and Bharat Petroleum Corporation Limited to set up 2G bio-refineries. Enzymes would be the key to making these 12 proposed plants successful. For this, the oil companies have partnered with academic institutions to produce efficient and cost-effective enzymes for 2G ethanol production.
Faridabad-based DBT-IOC Centre for Advanced Bio-Energy Research has evaluated a process to convert biomass to ethanol, utilising glycan hydrolases developed at the centre, in a demonstration plant under construction. The plant can process 10 tonnes of biomass a day. Earlier in 2024, Chennai-based Anna University and HPCL's Bengaluru-based HP Green R&D Centre signed an agreement to scale up a process developed by the university for cellulose enzyme production used in cellulosic ethanol (2G ethanol) manufacture. Syed Shams Yazdani's research group at the New Delhi-based International Centre for Genetic Engineering and Biotechnology has also developed a cellulase enzyme technology for 2G ethanol production (Designer Genomes).
Many new start-ups are also working in the biofuel segment. Bengaluru-based GPS Renewables turns organic food wastes into biogas and is testing if it can be used to charge electric vehicles. Delhi-based KNP Arises collects used cooking oil, which it converts into biodiesel and sells to consumers. Using a fully developed indigenous technology, Maharashtra-based Greenjoules makes diesel-like and petrol-like biofuels with agro-industrial wastes. Start-ups are working on various kinds of waste and producing different types of biofuels. Some have been concentrating on current needs such as ethanol, while others are working on developing future fuel technologies.
FUTURE FUELS
For future needs, hydrogen is a promising candidate. It is a sustainable vehicular fuel because of its potential to offer a clean, efficient, and versatile energy solution. Preetam Singh, a chemist by training and currently an Associate Professor at Indian Institute of Technology (BHU) Varanasi, has developed a reactor that produces this future fuel along with liquefied natural gas (LNG), carbon dioxide, and bio-coal (smokeless coal) from biomass. With the reactor recording encouraging results on a small scale in his laboratory, Singh has been assisting Varanasi-based Aranayak Fuel and Power to set up a mega plant in his hometown, Mirzapur, in Uttar Pradesh. By using his technology, they hope to produce 1 tonne of hydrogen, 3.5 tonnes of LNG, and 7.5 tonnes of bio-coal from 3.5 metric tonnes of biomass waste.
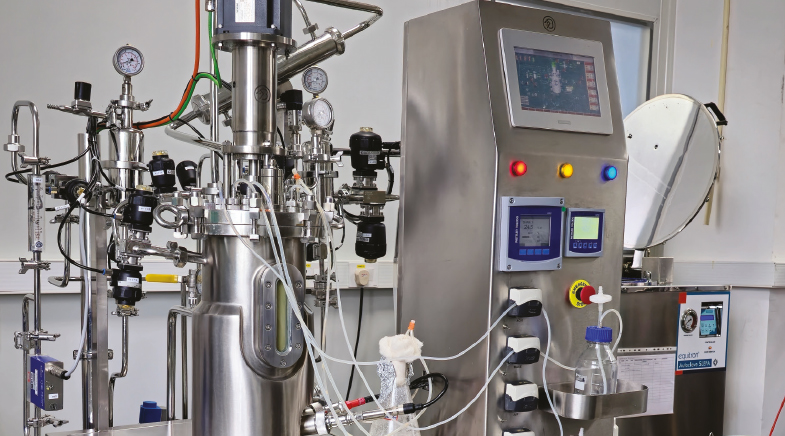
The technology, Singh claims, conducts in one day decomposition reactions that took millions of years on the Earth's crust to produce fuels such as petroleum, coal, and gas. The ₹50-crore mega reactor requires just 25 kWh of power to operate and can process 300 kinds of biomass waste — such as food waste and crop residues of wheat, rice, cotton, sugarcane, pearl millet, maize, and barley — with 45% efficiency. It is expected to start operation in a few months. Singh is a mentor to Biezel Green Energy, a start-up that is commercialising the reactor technology.
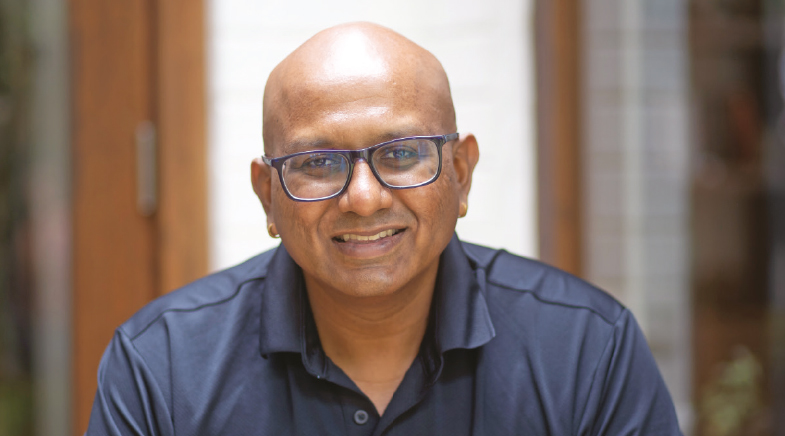
Singh had gained years of experience in batteries, fuel cells, and catalysts in Indian and foreign laboratories before setting up his laboratory at IIT (BHU) in 2016. Plants, he believes, are the best solar cells that capture solar light, carbon dioxide, and water and convert them into biomass, which has a high calorific value. However, he had to find an efficient way to convert biomass into usable fuels.
Fermbox Bio was able to tweak the fungus to produce the large quantities of enzymes required to produce sugar from agri-waste.
There are two ways to get biofuels from biomass: via microbes, and through a thermochemical route. He chose the latter because of his specialisation. Singh designed a reactor where the temperature and catalyst were his allies in converting biomass to biofuels. The reactor also has low electricity consumption. "For 1 kg of wood we use only 1 kilowatt of electricity but get 3.5 kilowatt in return," he explains.
The biomass is fed from the top end for processing, and the reactor is sealed to carry out the processing in an oxygen-deprived environment. Next, the temperature of the reactor is raised to 200-300°Celsius. This temperature, along with a catalyst, leads to a reaction where biomass produces carbon dioxide and hydrogen. Raising it further to 300-600°C leads to the release of methane gas and above 600°C, bio-coal, a solid carbonaceous material, is obtained. This can be used in tandoors and chulhas for cooking.
The challenge is to sort the mixture of gases — carbon dioxide, hydrogen, and methane. Ammonia or amine is used to absorb carbon dioxide and this mixture comes out in a liquid form, which is again heated to get back carbon dioxide that can be supplied to the beverage industry. The remaining mixture of methane and hydrogen is passed on to the cryo-separation unit, where the methane liquefies and hydrogen separates as gas. The liquefied methane is LNG and can be used for cooking, heating homes or generating electricity. Likewise, hydrogen gas can also be filled in cylinders and sold for use in oil refining, ammonia production, and methanol production. Singh believes that such plants will become more profitable in the future when hydrogen gas-powered vehicles hit the road.
See also:
Have a
story idea?
Tell us.
Do you have a recent research paper or an idea for a science/technology-themed article that you'd like to tell us about?
GET IN TOUCH