They're building in space!
-
- from Shaastra :: vol 03 issue 09 :: Oct 2024
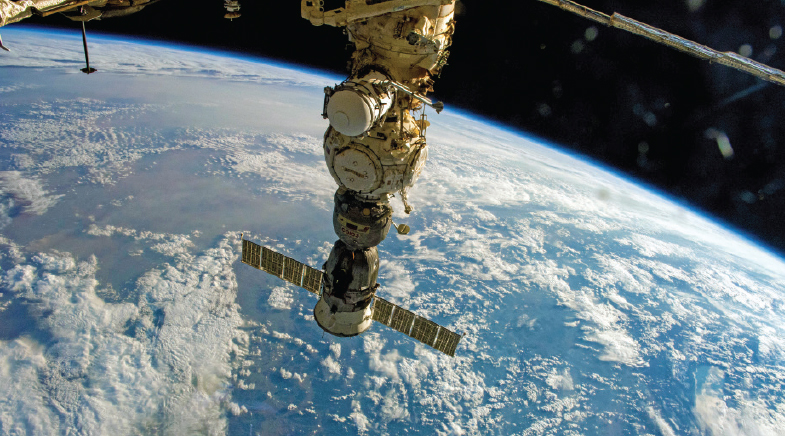
Researchers and engineers are looking at space as the new frontier to manufacture crystals, optical fibres and drugs.
For two-and-a-half seconds at the drop tower in the National Centre for Combustion Research and Development, gravity ceases to exist. In these 2.5 seconds Adhithya A., a post-doc scholar at the Indian Institute of Technology (IIT) Madras, which hosts the centre, manages to join two pieces of metal with a single weld bead. The 30.5-metre-high drop tower is India's only facility to replicate a microgravity environment – with near-weightlessness – for a short duration, and Adhithya has been using it to answer a singular question: what can we build in space?
Adhithya is part of the extraterrestrial manufacturing (ExTeM) team at IIT Madras, which explores what life in space would look like. "Whatever we do is with the vision of long-term settlements in space: what if Earth is no longer the only option?" says Sathyan Subbiah, a Mechanical Engineering Professor leading the ExTeM team. For the team, space engineering began with making something on Earth and putting it into orbit. This is what they call Space 1.0. The next step, Space 2.0, would be building in space, either for use in space or to bring it back to Earth.
MULTIPLE USES
The idea of manufacturing in space has fascinated humanity since the 1960s, with Russian scientists attempting vacuum-welding in space. The launch of the International Space Station (ISS) in 1998 allowed scientists to perform experiments in microgravity, and also study its effects on the human body in the long term. Without a budget to access the ISS, India decided in 2019 to build its own space station by 2035. "Moreover, ISRO also has plans to put humans in space with the Gaganyaan mission later this year. So, this is the right time to be developing techniques to build in space," says Subbiah.
The first project for ExTeM is to find a material to build extraterrestrial habitats that could protect humans from extreme environments. Its focus is to build in situ using regolith, the loose rocks and dust that cover the surface of a celestial body. While the team didn't have access to Martian soil, it recreated its composition based on its spectrometer analysis. "The problem with concrete available on Earth is that (it needs) water in a particular ratio to cure. We don't have that in space. That's why we came up with a formula where we mix Martian soil with sulphur," says Adhithya. The concrete can withstand compression matching earthen standards, and temperature ranges from 0 to 60 degree Celsius. "We are now testing for negative temperatures," he adds.
This follows the research at the Indian Institute of Science (IISc), Bengaluru, in making 'space bricks' by mixing simulated Martian soil with microbes that produce biopolymers, reducing their porosity and strengthening them. Aloke Kumar, Associate Professor in the Department of Mechanical Engineering, and his team at IISc have been studying bacterial activity in microgravity conditions.
While IISc has been geared towards building material in orbit, the University of Delaware in the U.S. has turned its attention towards biomanufacturing. With astronauts being sent to space stations for a long duration of time, Mark Blenner, Associate Professor in the university's Department of Chemical & Biomolecular Engineering, has been using microbes to bioengineer essential nutrients, medicines and vitamins on the ISS. It falls under the research programme B-SURE (Biomanufacturing: Survival, Utility and Reliability beyond Earth), funded by the Defense Advanced Research Projects Agency (DARPA).
It was under this project that Richa Guleria met Blenner for post-doctoral research. Having worked on developing extracellular proteins in bacteria for pharmaceuticals as a research associate at IIT Delhi, Guleria wanted to see if she could start producing proteins in yeast. Blenner's lab had a project on manufacturing nutrients in space using yeast, which she took up.
"Whenever NASA sends astronauts to space, a huge cost goes towards equipping them with any dietary supplements, vitamins and medicines," says Guleria. "Their expiry date changes in space; what is supposed to last three years may expire in six months. So, we can't stock everything in bulk, the storage is limited as well." Restocking supplies by sending a cargo shipment to space would prove costly, and one major way to mitigate these costs would be to promote in situ biomanufacturing.
For this study, Guleria had to analyse how various gravitational forces – microgravity, lunar gravity and Martian gravity – elicit different growth and stress responses in yeast. She did so by freezing batches of yeast and sending them up to the ISS, where they would be inoculated by astronauts. The first product molecule they targeted was beta-carotene, a precursor to vitamin A whose antioxidant properties would help protect against radiation in space.
The team was able to produce 20-25% higher levels of beta-carotene in yeast in zero gravity than on Earth. "That is a big achievement for us, given that it grew in sub-optimal conditions: in an anaerobic environment, without a special incubator to maintain a higher temperature," says Guleria.
IN SPACE BUT FOR EARTH
Space exploration is an area that interests governments, and so, building in space, for space, has received national attention for a while now. However, this decade brought in privatisation of space research, and for corporations, the goalpost has shifted back to Earth: can we build material in space and sell it back here, for greater profits?
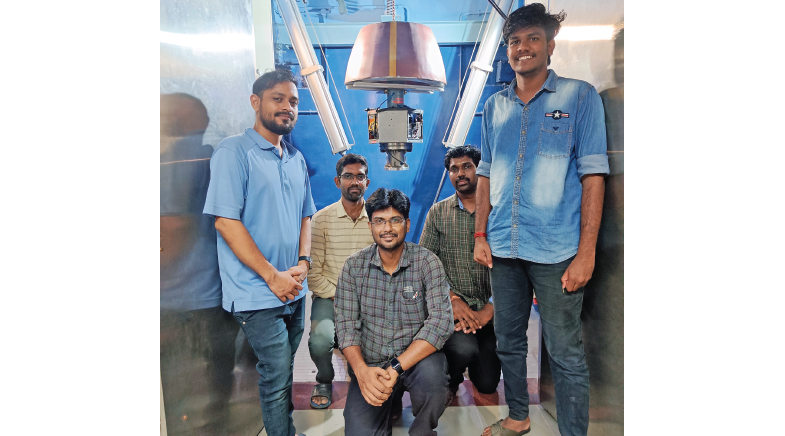
The answer to this question lies in two shifts in the space economy happening at the same time. The first is the increasing access to space, via reusable rockets that increase the number of launches into orbit every week. This means that products could be manufactured in space and also brought down to Earth rapidly enough to create a market. The second is the planned deconstruction of the ISS by 2030. The imminent absence of a government-funded space station leaves space for private companies to slide in, and set up their own stations and laboratories for corporations to research and manufacture in. This would be worth the money only if the product created in space was of much superior quality, as compared to the ones created on Earth.
Indian start-ups are in the process of building unmanned space labs to conduct research in manufacturing and biotech.
"A flame has its classic spade shape due to gravity," says Subbiah, pulling out a picture of a candle flame. "The hot air rises to the top, carrying the soot with it. This is due to convection, which is absent in microgravity. So, in space, the flame doesn't have any preferential direction to go towards, it becomes spherical."
This lack of convection and sedimentation in the microgravity environment becomes important in processes that involve crystallisation, such as the production of semiconductors and optical fibres. Crystals formed in space are more uniform and defect-free. This is the second leg of ExTeM's work; Subbiah is focusing on creating heavy metal fluoride glass, like ZBLAN, and will be testing the proof of concept to improve the purity in parabolic flights by the company Zero-G, next year.
"Optical fibre material like ZBLAN is used to transfer signals. If crystallites form inside the fibres, they will start absorbing various wavelengths of light inside, causing a loss rate. But if you produce them in space, the fibres are fairly clean and there are lower losses," he says. This eliminates the need for repeaters to boost the signals, lowering costs.
Earlier this year, Flawless Photonics, a Luxembourg-based company, became the first to draw over 11 kilometres of optical fibre in orbit. It is working with Axiom Space, an in-space manufacturing company in Texas, to improve the fibre further by making the raw material in space as well. Axiom Space works with manufacturing companies and biotech firms to take their science into space. It has found its niche in growing bulk crystals in space, bringing them back to Earth, slicing them into thin wafers and selling them to chip manufacturers.
Divya Panchanathan, Business Development Manager for Axiom Space, says that the idea is to "grow a small but significant quantity in space, and then utilise it for multiple products or devices on the ground". Axiom Space is also looking at growing 2D metal organic frameworks, which are made of conductive nanomaterials like graphene, and are difficult to grow beyond the 10-nanometre size on Earth. "We are also interested in leveraging the vacuum in space for semiconductor processing," she adds.
BETTER DRUGS, MORE PROFITS
Most in-space manufacturing companies are currently at the inflection point where they are testing proofs of concept and waiting to go into full-scale production. For a company to be profitable, it will have to find a niche in manufacturing products that are low-quantity but of high value. Based on the TechConnect conference Subbiah attended in Washington D.C. in 2024, he thinks venture capitalists may consider space biotechnology as an area with good potential. Tissues that are similar to different parts of the body are required for drug testing. "Growing those tissues is difficult here; they think they can make them in space and bring them back while still making money," he says.
Varda Space Industries, co-founded in the U.S. by Will Bruey, a former SpaceX engineer, focuses its business on microgravity-enabled pharmaceuticals. Company spokesperson Alex Pearlman says, "Pharmaceuticals are light, they don't need big machinery and we have been able to miniaturise traditional formulation technology into our capsule... It's the only industry right now on Earth that makes economic sense for in-space manufacturing."
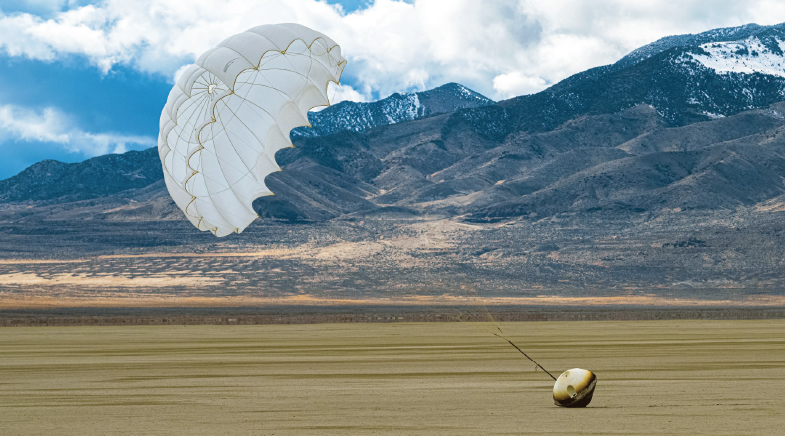
Varda Space collaborates with pharmaceutical companies to reformulate and improve their manufacturing processes in space, in a way that increases the bioavailability of drugs. In microgravity, polymers and proteins can be produced with uniform crystal distribution in new polymorphic forms. Kanjakha Pal, Senior Process Engineer at Varda Space, says: "Our goal is to improve the particle size distribution of drugs to make them more bioavailable even in smaller doses, so that patients will end up having to go to the clinic fewer times for the drug to be administered by a physician."
In fact, in 2018, the pharmaceutical company Merck demonstrated this possibility by reformulating Keytruda, an anti-cancer drug, in space, and was able to change the administration of the drug from an intravenous drip to a sub-cutaneous injection, which could be done at home as well. Meanwhile, research company LambdaVision has been experimenting with creating protein-based artificial retinas in orbit to restore vision for people with retinal degenerative diseases.
As for Varda Space, in February 2024, the company tested its capabilities by manufacturing ritonavir, popularly used in HIV medication. "This drug was known to have crystallisation problems for a long time, due to its polymorphism (that is, it can take up different lattice shapes)," says Pal. Researchers from Varda Space had discovered Form 3 of ritonavir on Earth, and as a demonstration of its technology, it managed to produce a stable version of it in space and bring it back to Earth, extract the drug from the capsule and send it to a lab, without any damage. "We had a capsule dropping out of orbit through the atmosphere, hitting temperatures three times hotter than the surface of the Sun. But we found that the most extreme environment these crystals endured was during their journey in the delivery truck!" says Pearlman.
The company offers testing on a hyper-gravity platform – a centrifugal machine that can increase the gravitational force up to 5g. The wide bandwidth of force helps researchers chart out the gravity sensitivity of the crystallisation process in different proteins, how it affects the growth kinetics and the polymorphic forms they can produce. "This helps our partners decide whether or not gravity is their problem or if they have a different formulation issue," says Pearlman.
In the coming decade, as launch cadence goes up and its cost goes down, the costs associated with manufacturing in space will go down as well, believes Pearlman. "In the near future, we will be manufacturing crystals in factories in space, just as we do them on the Earth," she says.
COMING UP: INDIAN SPACE LABS
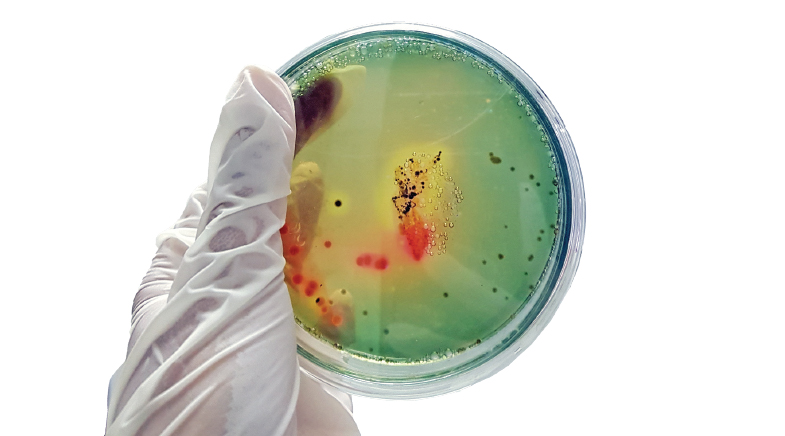
Indian start-ups like Vellon Space in Bengaluru and Space Rickshaw in Chennai are in the process of building unmanned space labs to conduct research in manufacturing and biotech. Ajay Kumar, Founder of Vellon Space, is working with G.K. Suraishkumar, Professor of Biotechnology at IIT Madras, to conduct biological experiments in space. Suraishkumar's team will test the devices Vellon puts together. Bacteria, for example, grow better in space, and that would help improve the purity of drugs we can get, says Kumar. "India has a big diabetes problem and it would be great if we could make insulin pure enough for patients to take just two or three shots every year."
Have a
story idea?
Tell us.
Do you have a recent research paper or an idea for a science/technology-themed article that you'd like to tell us about?
GET IN TOUCH