Breaking ground
-
- from Shaastra :: vol 04 issue 03 :: Apr 2025
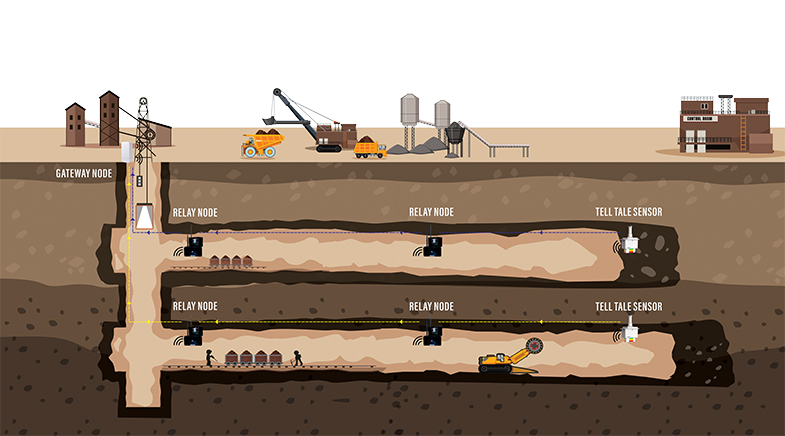
Digital technologies are streamlining operations and improving safety measures in mines, saving time, money, and lives.
When Mohit Sahu saw the harsh and rugged environment of a mine on his first field trip to a site in 2013, he decided that a career in mining was not for him. Three years later, he recalled that visit as he surveyed another mining site, this time looking at ways to improve mining conditions.
Sahu had joined a B.Tech programme in Mining and Mineral Engineering at the National Institute of Technology Raipur, mainly because his family felt that a career in mining would keep him close to his home in Raigarh district in Chhattisgarh. But reckoning that he was not cut out for mining, Sahu, with his friend Puru Agrawal, started developing software and services-based businesses for the Chhattisgarh government after graduating.
And, then, life came full circle. In 2016, he was back at an excavation site with his mining industry friends, who had asked him for ways to synchronise the 3Ms — men, machine and material operations — at the coal mine. Sahu saw where the problem was. "There was no collection of data. They were still using pen and paper," says Sahu, who believes that this critical failing led to a communication gap at the mining site, raising safety issues and affecting productivity.
To solve this problem, his team at their start-up, Minocular, retrofitted Internet of Things (IoT)-enabled sensors on machines to track and record their activity status and output. They devised a platform to schedule labour tasks based on workers' expertise to ensure high productivity of operations. To keep a tab on the activities of mining sites, the team developed a drone (called MinoDrone) with a vision sensor that captured aerial shots used for generating 2D and 3D maps of a site, displaying the location of slopes, haul roads, and so on. Since the contours of a site change as work progresses, drone data providing greater resolution and on-demand monitoring are considered more relevant than satellite data. The visual data from the drones keep tabs on and help coordinate different activities on the sites, planning and locating blasting and drilling sites, tracking the movement of fleets, and identifying possible blockages. This feed from drones is also processed to check if the site has been following regulatory requirements — such as haul width — laid down by mining authorities. "Doing such surveys manually takes at least one month; with a drone, you can do this within two or three days," Sahu says.
Entrepreneurs such as Sahu are changing the unsafe and labour-intensive image of mining sites that unearth coal and other resources. Today's smart mining sites are equipped with drones tracking mining activity, IoT-fitted interconnected machines and equipment, autonomous (driverless) and semi-autonomous trucks carrying materials, paperless operations and real-time remote monitoring. Drone technology for mapping and surveying has gained widespread acceptance across the sector, Sahu says.
PAST ISSUES - Free to Read
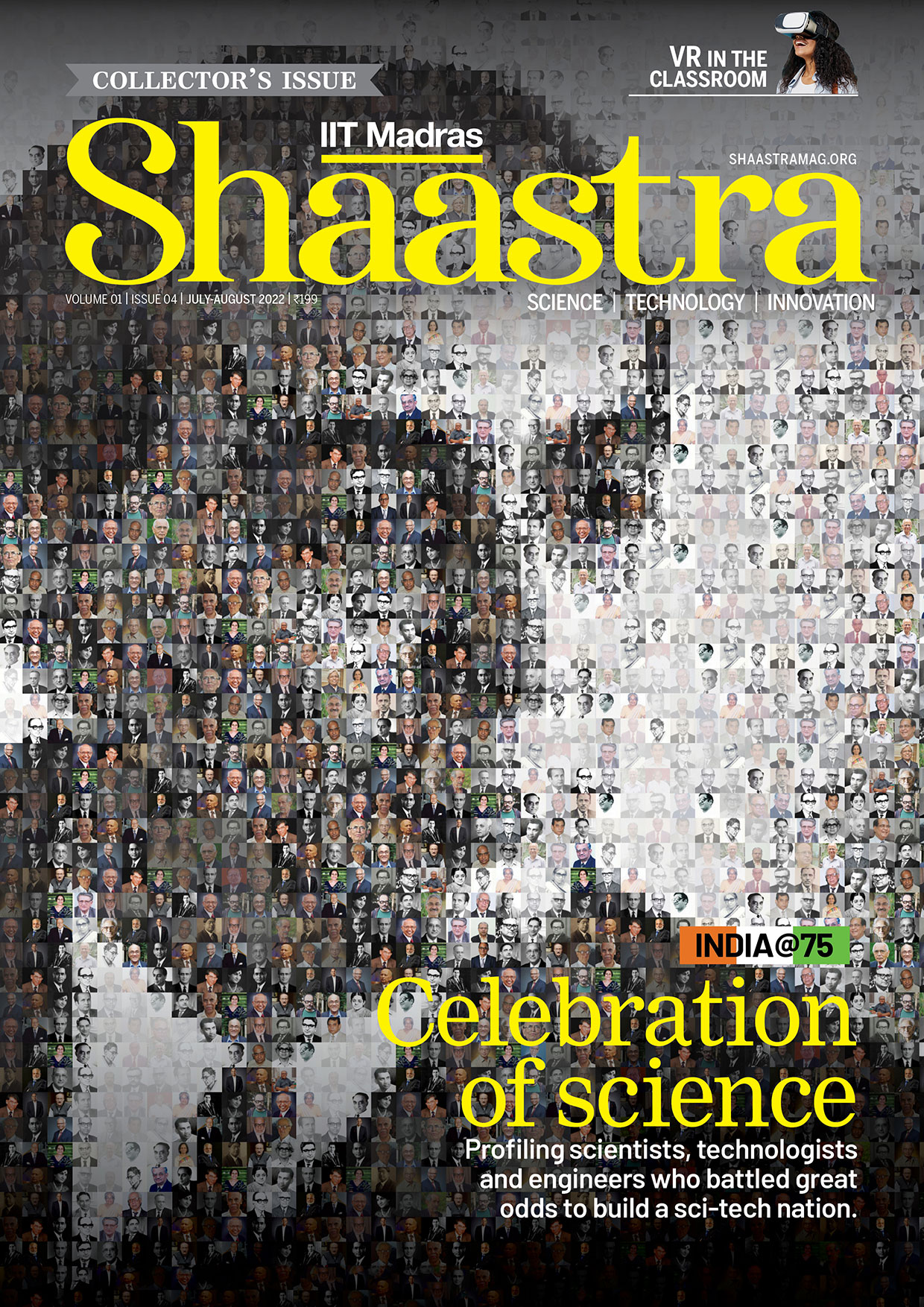
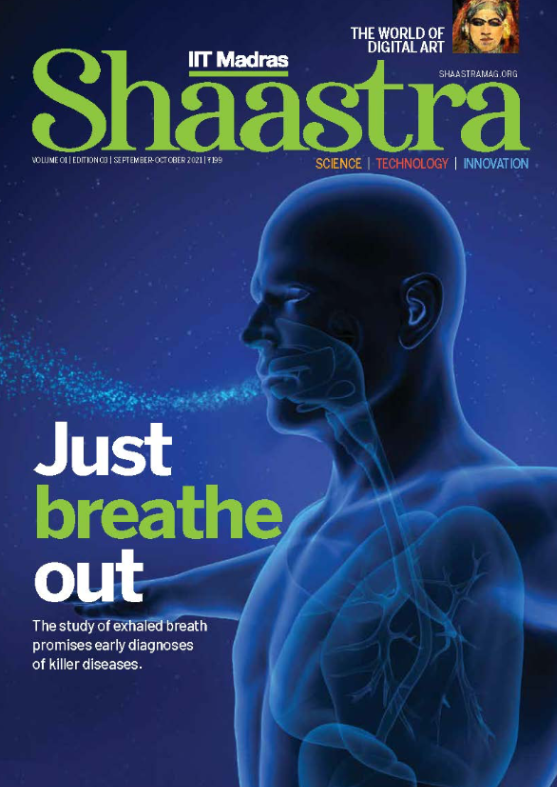
Have a
story idea?
Tell us.
Do you have a recent research paper or an idea for a science/technology-themed article that you'd like to tell us about?
GET IN TOUCH