No taste for waste
-
- from Shaastra :: vol 02 issue 02 :: Mar - Apr 2023
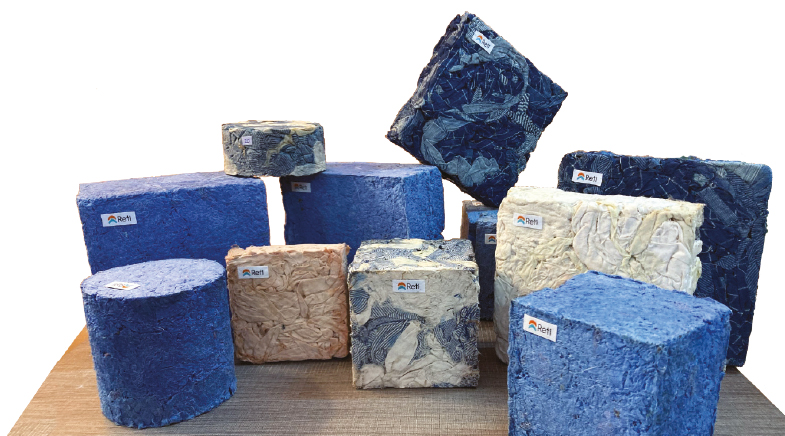
Entrepreneurs are looking at saving time, money — and lives.
RETI ECOTECH
Founders: Jahnavi Rao and Indrayani Kadu
Year: 2021
Big idea: Using textile waste to make construction material
Textile waste in India gets dumped in landfills and clogs storm water drains and sewer lines. It was to tackle this environmental problem that engineers Jahnavi Rao and Indrayani Kadu decided to start a company that would use this waste to make construction material.
At their venture Reti Ecotech, incubated at the Society for Innovation and Development at the Indian Institute of Science, Bengaluru, Rao and Kadu plan to use textile waste to make different types of construction material: wall panels, room partitions, false ceilings and furniture, and for acoustic and thermal insulation.
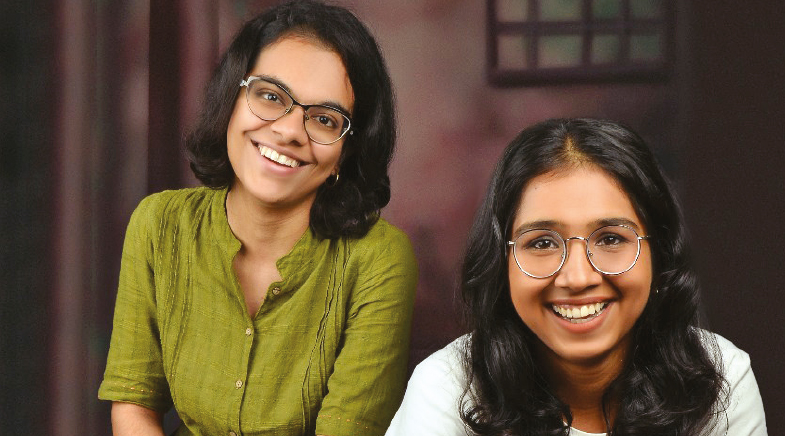
Rao, who has a Master's in Biomedical Engineering from the U.S., and Kadu, who did her post-graduation in Nanotechnology from Belgium, met while working in a medical diagnostics company in Bengaluru. During their lunch-break conversations, they discussed how they could use technology in the sustainability space — and realised that nothing much was being done about textile waste. According to Kadu, less than 10% of the textile waste generated in the country is recycled.
They spoke to Saahas Zero Waste, a waste management company in Bengaluru (see bit.ly/3IogBZy), and concluded that eliminating such waste was not easy. With no other viable option, a large quantity of textile waste is incinerated, which adds to pollution. So, the two decided to start a venture that would work on converting textile waste into construction material.
"We realised that textiles inherently have properties such as acoustic or thermal insulation and ductility that we could leverage," Kadu says. Cement bricks, she points out, are highly brittle. "If you reinforce them with textile waste, you can increase the toughness of the material," she adds.
Rao explains that they did not look at textile waste merely as waste but as another kind of raw material. The raw material had some properties, and the two studied how they could use those properties to make their products function better.
Reti — derived from the Marathi word rete for fine sand — worked on the concept, and developed a few prototypes for different applications. The company mixes shredded textile waste with a proprietary binder that is put through a hydraulic press. It then uses a mould to convert it into products for the construction industry. "We play around with the binder for the compression level for different applications," Rao says.
The company has been working on grants and plans to conduct pilot studies for various products, which they hope to commercially launch next year. They estimate the global market for partition walls and false ceilings at $45 billion and the Indian market at $260 million. The global market for insulation materials is worth $14 billion and the Indian market, $120 million.
SOLINAS INTEGRITY PVT LTD
Founder: Divanshu Kumar, Krishnan Balasubramanian and Prabhu Rajagopal
Year: 2018
Big idea: Using robotics to put an end to manual scavenging
The Professor in the Department of Mechanical Engineering at the Indian Institute of Technology (IIT) Madras had given his students a task: develop a robot to clean septic tanks. Divanshu Kumar, who has a degree in Mechanical Engineering and a Master's in Product Design, began working on the project, and saw "good signs" of success.
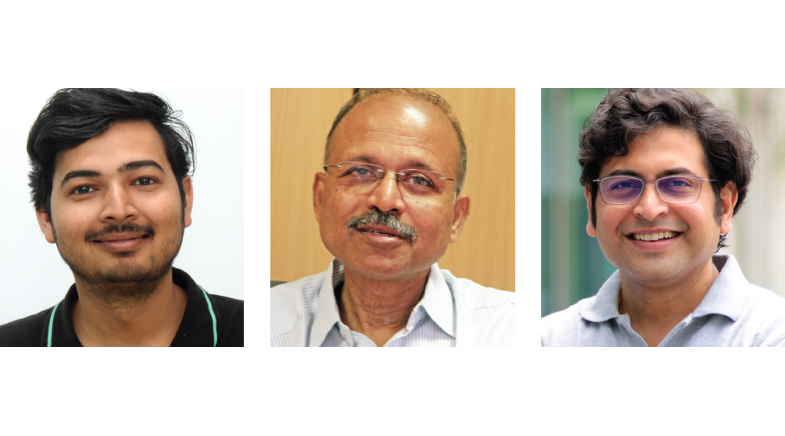
Divanshu Kumar (left) set up Solinas Integrity Pvt Ltd with Professors Krishnan Balasubramanian (centre) and Prabhu Rajagopal (right); its products Endobot (below) detects leaks in pipes, and HomoSEP cleans septic tanks.
PHOTO: BY N. RAMAKRISHNAN/BY SPECIAL ARRANGEMENT
Kumar went on to set up a company — Solinas Integrity Pvt Ltd — with Professor Krishnan Balasubramanian and Professor Prabhu Rajagopal, both from the Mechanical Engineering Department at IIT Madras. It was Rajagopal's problem statement that led Kumar to develop a robot to clean septic tanks. Kumar says that once he'd finished the project, they realised it had commercial potential, and Solinas was founded.
Kumar believes that while attention is focused on the manual cleaning of sewer lines, the bigger challenge lies in the manual cleaning of septic tanks, a process that often leads to deaths due to asphyxiation because of the high concentration of sludge in such tanks. While Solinas designed its mini robot to deal with septic tanks, it also worked on ways to detect leaks in water pipelines. It now has two products — one to clean septic tanks and the other to detect leaks in water and sewer lines.
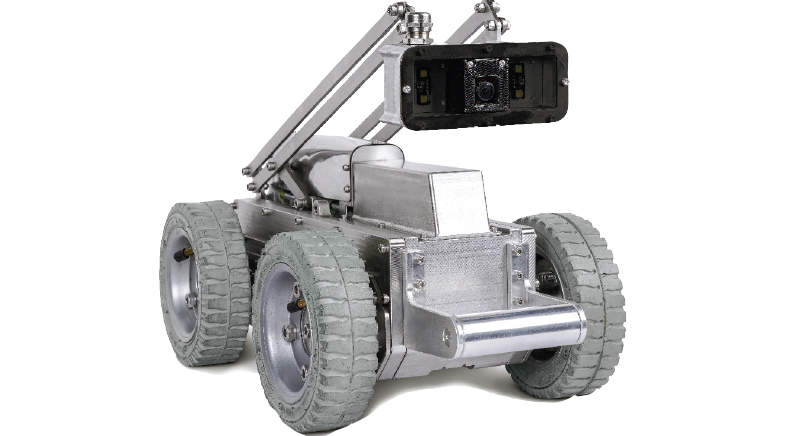
Endobot
After almost two years of research, Solinas launched its first product — Endobot — in mid-2020. The robot is small enough to crawl into a pipeline of a 100-mm diameter and can go up to a distance of 200 metres. The challenge in developing this product was to miniaturise the motor, develop a printed circuit board (PCB) that would sit on the robot and optimise the mechanical design. The robot is 15-18 cm long and about 8.5 cm wide.
According to Kumar, Endobot can be deployed in water and sewer lines to detect leaks through live visual feeds without having to dig trenches. It can help reduce the wastage of huge volumes of water in pipelines. It uses high-profile cameras with image processing, and through constant condition assessments and analyses, Solinas helps maintain the integrity of the pipelines. The company provides Endobot as a service.
The second product — HomoSEP, launched in mid-2021 — homogenises sludge that has settled at the bottom of a tank and become hard. The slurry is pumped out with an integrated suction mechanism. This robot helps in cleaning sludge without humans having to enter a septic tank. HomoSEP has an inverted umbrella kind of a structure that opens up after entering the narrow opening of a septic tank. Its blades mix the sludge, making it easier to be removed. Solinas has sold seven HomoSEP robots so far and has orders for over a dozen more.
SIMYOG TECHNOLOGY PVT LTD
Founders: Dipanjan Gope, Anant Devi, Bibhu Nayak and Harikiran Muniganti
Year: 2017
Big idea: Simulation software to help electronic hardware manufacturers detect defects at the design stage
A Bengaluru-headquartered company is helping manufacturers of electronics spare parts save money — and time. SimYog Technology has developed a virtual laboratory that allows them to test parts for defects early on in the design stage.
Electromagnetic interference and electromagnetic compatibility are problems that contribute significantly to compliance failures for electronics and electrical hardware parts. Electronics parts may appear to work well in isolation, but when placed in what is called a noisy environment — electromagnetic noise — as in an automobile, they may start malfunctioning.
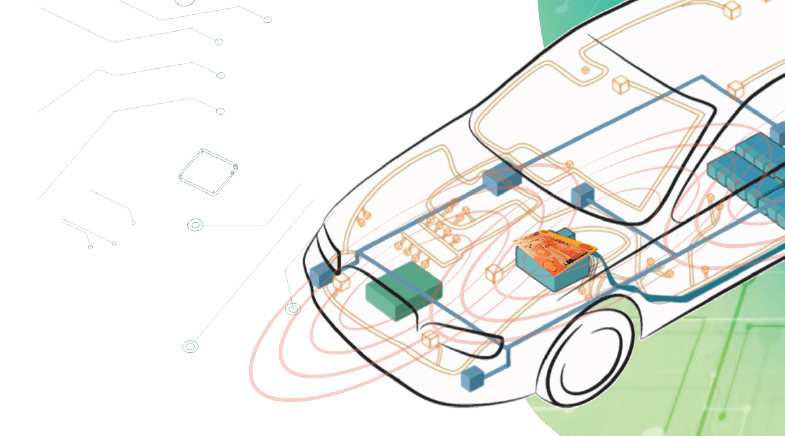
Traditionally, automobile manufacturers require that parts makers get such components tested in a physical laboratory before they place orders. If any of the parts is found to be defective, the suppliers have to go back to the drawing board and come up with a fresh design and go through the whole time-consuming and expensive process again.
"Our value proposition is a virtual laboratory enabled through simulation," says Dipanjan Gope, co-founder and CEO. Traditionally, he adds, this was a physics-based simulation. "We are trying to also use data-based models to handle such a complex problem."

SimYog Technology co-founders (from left) Anant Devi, Harikiran Muniganti, Bibhu Nayak and Dipanjan Gope have developed a virtual laboratory that tests electronics parts for defects.
PHOTO: BY SPECIAL ARRANGEMENT
Why is it complex? It is because there are multiple printed circuit boards (PCBs), with many components and cables. Computational time- and memory-wise it is a challenge, says Gope, adding that the company is "handling" this problem.
Gope, who has a B.Tech in Electronics and Communications Engineering from IIT Kharagpur, and a Master's and a PhD from the University of Washington, met his three co-founders at the Indian Institute of Science (IISc) in Bengaluru. The initial R&D was done at IISc between 2014 and 2017, with the help of grants and industry collaborations. Algorithms and basic prototypes were developed during this period. SimYog released its first product in 2020.
Electronics parts may appear to work well in isolation, but may start malfunctioning when placed in a noisy environment.
SimYog's product is an enterprise software, where its customers have to load their design that includes all the information of the PCB and its components, after which an analysis is given.
The company is now focusing on the automotive space. Nearly 60% of its customers are outside India. The percentage of electronics and electrical components has been steadily increasing in automobiles, making it a challenge for parts manufacturers and providing an opportunity for SimYog, which helps them to figure out defects.
Have a
story idea?
Tell us.
Do you have a recent research paper or an idea for a science/technology-themed article that you'd like to tell us about?
GET IN TOUCH