Cleaning up their act
-
- from Shaastra :: vol 01 edition 03 :: Sep - Oct 2021
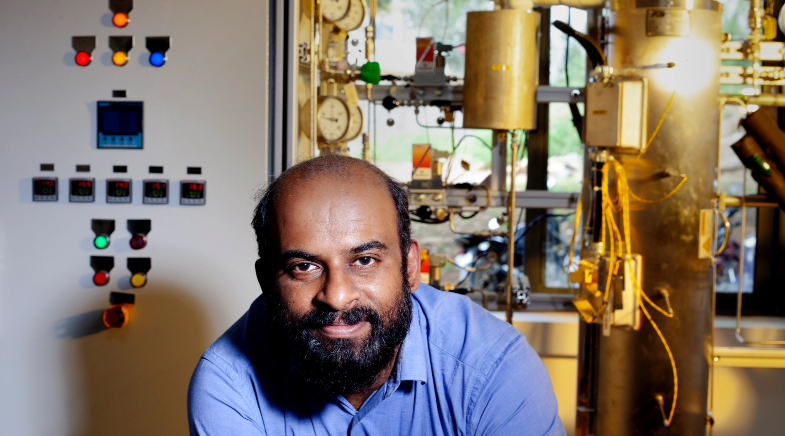
Indian companies and research laboratories are working on innovative systems to remove carbon dioxide from the atmosphere.
The research team at Breathe Applied Sciences Private Limited was looking forward to travelling to the U.S., all ready to demonstrate its carbon utilisation technology for the international Carbon XPRIZE. The competition required participants to showcase a material or technology that could capture carbon dioxide - the heat-trapping gas that contributes to global warming - and convert it into useful products.
Then COVID-19 struck.
"We were lucky to get support from an angel investor who was ready to fund this expensive trip that required instruments to be taken along. We were all set," says Sebastian C. Peter, Professor at the Jawaharlal Nehru Centre for Advanced Scientific Research (JNCASR), Bengaluru.
Peter had founded the start-up in 2016 on the JNCASR campus since only private companies could participate in the prestigious global competition. The company was among the top ten finalists and the only Indian company to reach the finals.
With the pandemic, flights and events came to a halt. "We waited, waited and waited but travel did not resume," says Peter.
At the heart of the technology developed by Peter's team is a catalyst that can convert carbon dioxide to methanol, a clean fuel seen as an alternative to diesel and petrol.
The competition organisers then asked the start-up, which works in the area of carbon capture and utilisation, for data that would show the efficacy of its technology in India. In the last stage of the competition, the company was asked to demonstrate that its technology had the potential to convert at least 2 tonnes of carbon dioxide per day.
With factories and industries closed because of COVID-19, the company struggled to set up a plant. When it was time for the submission, it was able to demonstrate data for only 89 hours – against the required 720 hours. "We continued to capture data after the deadline and realised that, in terms of fuel production, we were number one," Peter says. "We could not win because the volume of data was not sufficient."
UTILISING CARBON
At the heart of the technology developed by the team is a catalyst that can convert carbon dioxide to methanol, a clean fuel that is considered an alternative to diesel and petrol. While similar technologies exist, the method developed by Peter's group has more than 70% efficiency (against the others' 25%). For the conversion to methanol, the carbon dioxide received from carbon capture plants, together with hydrogen in a particular combination, is fed over the catalyst at a high temperature and pressure.
While the catalyst patented by the start-up has an efficiency of 35-38%, the additional efficiency of about 35% is achieved by recycling the residual carbon dioxide and hydrogen for the same process again. The technology not only reduces the carbon in the atmosphere, but a cost analysis shows that the methanol produced is ₹10-15 cheaper than that manufactured in other ways.
This technology has a readiness level of 7 on a scale of 0-9, which means that a technology prototype demonstration has been conducted in an operational environment. The company is now in talks with various companies to commercialise the technology. The team has also found ways to produce other fuels such as dimethyl ether; the tests for those are in the laboratory stage.
Across the country, companies such as Breathe Applied Sciences are trying to develop catalysts that can produce methane, ethanol, ethylene, dimethyl ether, plastics and other fuels from captured carbon dioxide. However, carbon capture and utilisation (CCU) wasn't considered lucrative when it first came up in the 1990s.
CCU is an energy-intensive and costly affair because the process takes place at a given pressure and temperature and in the presence of a catalyst, points out Dr Malti Goel, chief executive at the Climate Change Research Institute, New Delhi.
"Therefore, the initial focus of the energy-constrained world was on carbon capture and storage (CCS)," adds Goel, formerly a scientist at the Department of Science and Technology and a member of the Indian CO2 Sequestration Applied Research (ICOSAR) Network. Since then, India and other countries have made strides in energy production technologies. Additionally, if this energy comes from renewables, it will make carbon utilisation industrial processes more sustainable.
CAPTURING CARBON
Before carbon dioxide is used to make other chemicals or sent for long-term storage, it has to be captured. Carbon Clean Solutions, a company started up in 2009 by two engineers from IIT Kharagpur and currently headquartered in London, has established 38 carbon capture plants across the globe, including one in India. Its plant in Thoothukudi in Tamil Nadu, set up with Tuticorin Alkali Chemicals and Fertilizers Limited, captures close to 60,000 tonnes of carbon dioxide a year from a nearby coal plant to produce soda ash, used in detergent, paper production, the glass industry and so on.
To capture the carbon dioxide, flue gas arising from the industrial plant is sent to a pre-treatment unit where nitrous oxides, heavy metals and other undesirable materials are removed. Next, this pre-treated gas enters a vertical absorber column. The gases are injected from the bottom and the chamber is showered with a patented solvent that absorbs carbon dioxide from above. When the solvent and carbon dioxide meet midway, the solvent reacts with carbon dioxide, which flows along with the solvent to the bottom, while other gases evaporate from the top.
The solvent with absorbed carbon dioxide is then taken to a second chamber, where it is heated at 120° Celsius, a temperature at which the carbon dioxide is released from the solvent. This purified carbon dioxide is then ready to be either stored or utilised. The company has around 55 patents that are related to the solvent, its use, process design and the size of the instrument.
While there is no dearth of materials known to capture carbon dioxide from industrial sources, the bottleneck in the use of carbon capture technologies is the need for large-sized equipment. This makes it cost-effective only for large industries. The company's R&D team has, therefore, been working on smaller equipment that can be used by small industries as well.
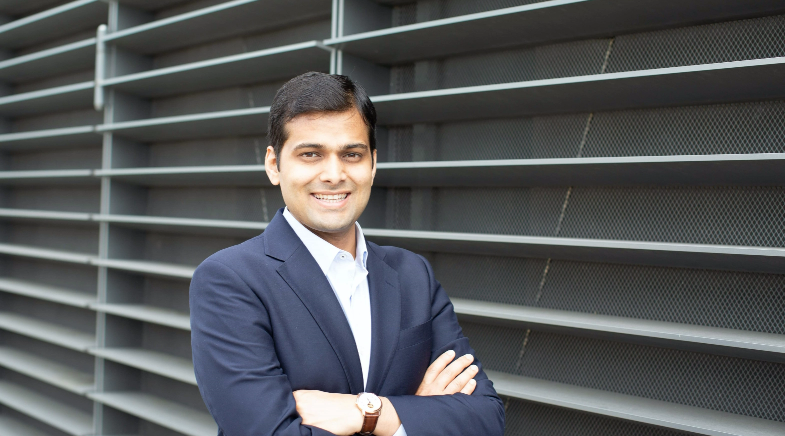
CAPTURING CARBON
"We have developed the technology that is reducing the size of the equipment to a tenth of what it was and reducing the footprint of the carbon capture equipment to a fifth of what it was. This makes the whole unit modular and skid-mounted so that it can be taken to any industrial site," says Aniruddha Sharma, CEO, Carbon Clean Solutions.
While small industries are the new focus, the company is working with established players such as Dalmia Cement and was recently awarded a project by NTPC to demonstrate carbon capture and utilisation at its power plant. It is also working with Tata Steel to set up a carbon capture plant at Jamshedpur Works to capture 5 tonnes of carbon dioxide per day.
Although the technology developed by Carbon Clean Solutions is a good way to limit the entry of carbon dioxide into the atmosphere, it is restricted to steel, cement, chemical and power plants. Many believe that direct air capture, in which carbon dioxide is captured straight from the air, is the technology for the future. An economically viable technology developed on these lines can help push for a net-carbon-zero world. However, developing such technology is an expensive proposition.
"Imagine capturing 400 molecules of carbon dioxide from one million air molecules. It is a tricky task and hence costly. But if we get a really good absorber or absorber material, we can succeed in this task," Goel says.
A recent breakthrough in this area was the launch of the world's largest direct air capture plant developed by Climeworks in Iceland. The plant can capture 4,000 tonnes of carbon dioxide a year; this is then injected into nearby basaltic rock formations and turned into stone.
SEQUESTERING CARBON
While many believe that capturing carbon and utilising it to make fuels is the way forward for carbon abatement, some feel that there are better, long-term methods.
"We may have a process where we can convert carbon dioxide into some usable chemical, but if the chemical itself is so usable and so valuable, why would one like to reduce the value of the chemical," argues Dr Rajnish Kumar, Professor in the Chemical Engineering Department at IIT Madras.
Hydrogen, he explains, is one such chemical. Hydrogen fuel is itself green, and thus its use in producing methanol in an effort to utilise carbon dioxide does not seem reasonable, he holds.
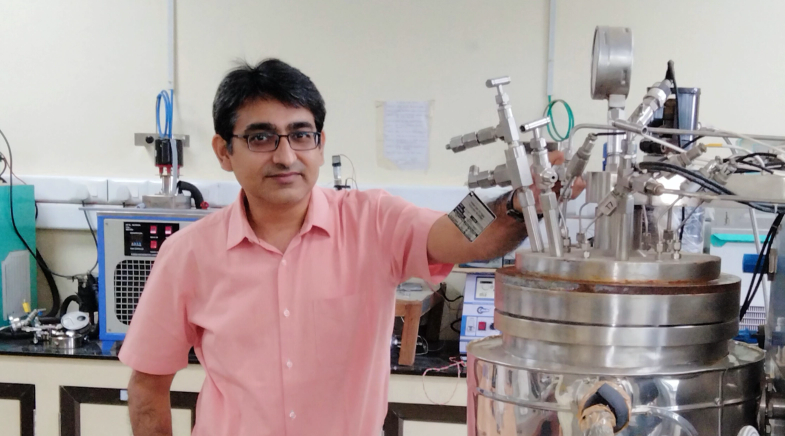
Kumar believes that carbon sequestration is the way forward, given the high rate of carbon emissions. Carbon dioxide can be sequestered at oil wells, saline aquifers, basalt rocks, abandoned coal mines, oceans, plants and soil.
His research group at IIT Madras has taken inspiration from the natural process of carbon sequestration in oceans and is working to mimic this process so that it can be used at a commercial scale. Essentially, carbon dioxide can exist as gas, liquid and solid depending on the temperature and pressure. Deep down in the ocean, at around 300 metres, the temperature and pressure are just right for carbon dioxide and water molecules to combine and form hydrates. These hydrates can stay in the oceans for millions of years without dissociating, locking up this greenhouse gas for a long time.
At a commercial level, the flue gas (which contains plenty of other gases along with carbon dioxide) from power plants and industries can be transported to the seabed via pipelines. When this flue gas reaches a depth of 300 metres, it will get the right conditions to form hydrates of carbon dioxide by reacting with water molecules.
Rajnish Kumar's laboratory is trying to find a way to replace the methane in hydrates under the sea with carbon dioxide.
This process of carbon dioxide hydrate formation may itself be slow or may be impacted by the presence of other gases in the flue gas mixture. Kumar's research work involves finding out additives that can hasten the process of hydrate formation and ensure that carbon dioxide molecules react with water to form hydrates and not with the other gases such as nitrogen, hydrogen and sulphur in the flue gas mixture.
In its laboratory, the team also studies if these hydrate structures stay stable to ensure that the carbon remains sequestered for a longer period under the sea.
His group's research is being funded by GAIL India Limited. The laboratory is also trying to find a way through which it can replace the methane in hydrates under the sea with carbon dioxide. This will have twin benefits: carbon sequestration, and recovery of methane fuel.
A Carbon Clean Solutions plant in Thoothukudi captures about 60,000 tonnes of carbon dioxide a year from a nearby coal plant to produce soda ash.
While sequestration looks like a good way to permanently store carbon dioxide, its transport from the point of its generation and capture to the place of sequestration may pose problems. "Carbon capture storage, which was once considered feasible, could not be pursued due to fewer potential storage sites in India. Geographically it is not feasible if source and storage sites are far apart," Goel states. Kumar, however, feels that carbon dioxide gas can also be transported the way LPG is being moved in pipelines.
INDIAN SCENARIO
India has three CCS plants, with negligible capturing capacity, that have been operating for decades and a CCUS (Carbon Capture, Utilisation and Storage) plant in Thoothukudi, and has plans for more. ONGC and Indian Oil Corporation have signed an MoU to evaluate the feasibility of India's largest CCUS project at the Koyali refinery in Gujarat. Other public sector companies, such as NTPC, BHEL and NALCO, are partnering with consultancies, companies and researchers to explore the feasibility of CCUS at their respective sites.
Private players such as Dalmia Cement, Tata Steel and Reliance Industries are working towards becoming carbon-neutral. On the R&D front, the country is part of Mission Innovation, a global initiative to accelerate the development of climate-friendly technology.
India was also an active member of the ICOSAR Network, set up in 2007 to initiate talks on carbon storage technologies. Despite these efforts, the country still lacks technologies that can be adopted by a company eager to reduce its carbon emissions.
While India remains committed to cutting down emissions, the recent report of the Intergovernmental Panel on Climate Change (IPCC) underlines the need for urgency, pointing to extreme weather events. As the pressure to abide by environmental agreements mounts, India is redrawing its strategy to cut down emissions. The country's renewable energy policy may be on track, but it does not have policies that push for the adoption of CCUS technology.
"While one can switch off coal-based power plants and shift to solar, hydro, wind and nuclear energy in a few years, if you think about industry – steel, cement, refining, chemicals - there is no option, and the only way, for now, is to decarbonise them," says Sharma of Carbon Clean Solutions.
However, the policies that give incentives to companies that capture carbon dioxide or penalise those that don't are not yet in place.
With various countries having already announced their timelines to achieve net-zero emission, all eyes are on India. It seems self-evident that the strategy to realise that green goal hinges critically on the adoption of CCUS technologies in the country.
ALL FOR CLEAN AIR
- CCUS (Carbon Capture, Utilisation and Storage) encompasses methods and technologies that remove carbon dioxide from its source or atmosphere and then either utilises it or stores it for the long term.
- CCUS technologies are a way to meet Paris Agreement goals for countries that are still heavily dependent on fossil fuels for power generation and cannot slow down high carbon dioxide-emitting industries such as cement, steel and fertilisers.
- According to the International Energy Agency's 2020 report, 20 major commercial CCUS plants are operating around the world and can capture up to 40 metric tonnes of carbon dioxide every year.
Have a
story idea?
Tell us.
Do you have a recent research paper or an idea for a science/technology-themed article that you'd like to tell us about?
GET IN TOUCH