Fine-tuned friction
-
- from Shaastra :: vol 03 issue 02 :: Mar 2024
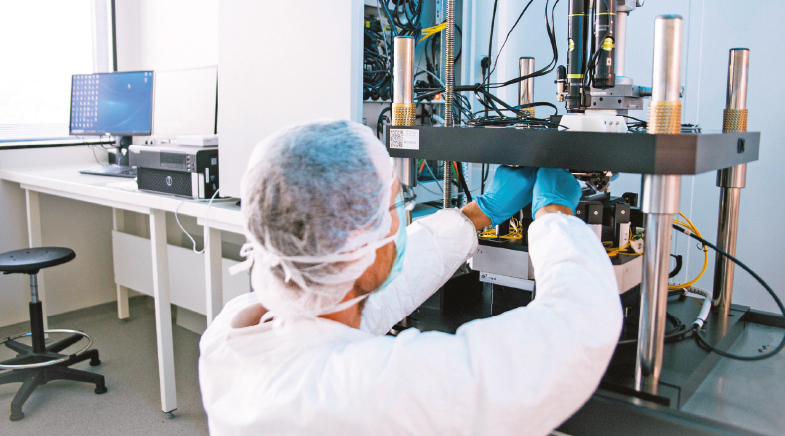
Make way for on-demand friction with a technique that promises to help in multiple fields.
The impact, by all accounts, will be significant. Scientist Julien Scheibert and his colleagues at the University of Lyon, France, have devised a technique that can fine-tune friction between two flat surfaces.
Friction is created when projections, or tiny bumps, on one surface collide with similar bumps on another, and force has to be applied to tide over this collision. It controls countless aspects of a person's life, from walking to driving. All moving parts — the hands of a clock, or turbines that rotate to generate electricity, for instance — experience friction. Friction is also critical in the design of modern electronic devices involving haptics such as those used in robotics and virtual and augmented reality settings.
Using engineering insights gained over decades, science has been able to devise strategies to minimise frictional forces on a surface interface. Such methods include lubrication and surface roughness modification. For centuries, however, scientists have been trying to comprehensively understand friction to be able to accurately predict frictional forces acting at the interface of two materials. But the sheer diversity of textures found on surfaces makes such predictions difficult. For a given surface, textures can span several orders of magnitude ranging from the atomic scale to millimetres.
A dozen or more parameters influence the interfacial conditions, and thus friction, explains Satish V. Kailas, Professor of Mechanical Engineering at the Indian Institute of Science (IISc), Bengaluru. These, he adds, can be classified into three broad areas — deformation mechanisms that take place at the interface; tribo-chemical reactions between atoms present in both the surfaces; and the influence of debris produced due to constant rubbing of the two surfaces involved.
In 1779, Charles-Augustin de Coulomb, one of the founders of tribology (the science of friction), wrote about the interlocking of asperities, or bumps, on rough surfaces. Surface topography determines the amount of actual contact between two bodies, which typically touch only on the highest peaks of their topographies. The contact area of random interfaces increases proportionate to the applied load.
If friction can be removed in all working machines and mechanisms, the world will save an enormous amount of energy.
Now, the French research team led by Scheibert at the Laboratory of Tribology and System Dynamics in Lyon has devised an alternative strategy that rationally designs the frictional properties of interfaces. This strategy has the potential to help reduce the drawbacks of friction, minimising energy losses, wear and related maintenance operations.
The scientists achieved this by creating a flat surface with adjustable bumps. They reported the work in a recent issue of Science (bit.ly/metainterfaces). To create this surface, the team used a rubber-like elastomer called a metainterface. The bumps on the metainterface were designed in such a way that the height of each could be individually adjusted. By altering the heights, the researchers were able to change the amount of friction produced when pressed and moved against another flat surface.
"Frictional contacts play a functional role in many man-made devices, from shoe soles to syringe pistons, through robotic hands and watch mechanisms. The specifications on friction for those interfaces are usually ambitious and challenging to satisfy," Scheibert says. Mastering friction can help shoe soles get a better grip, he explains. "Every application has different requirements, and a generic and versatile design strategy like ours is a way to prepare contact interfaces with on-demand friction behaviour," he adds.
Surgeons working with artificial organs, for instance, will not just want the organs to have the right bulk elasticity, but also the right kind of friction with gloves or surgery tools. Improved mastering of friction will make it easier to adjust the surface behaviour. "Our design strategy significantly reduces the need for experimental calibration; once the material pair is fixed, we can address any friction specification and find the optimal solution on the first experimental try," he says.
Friction control in dry conditions mainly relies on two pillars: a careful choice of the pair of surface materials and modification of the surface roughness into well-defined topographies. "Unfortunately, the complexity of natural contact interfaces is such that the relationship between the physical characteristics of surfaces and their effect on the friction force remains poorly understood," Scheibert says.
REDUCING FRICTION
While Scheibert's team focused on frictional properties of metainterfaces, another international group of researchers led by Nikolai Brilliantov, who is on the faculty of the Skolkovo Institute of Science and Technology in Russia and the University of Leicester in the U.K., has shown how surfaces can be made so slippery that there is hardly any friction.
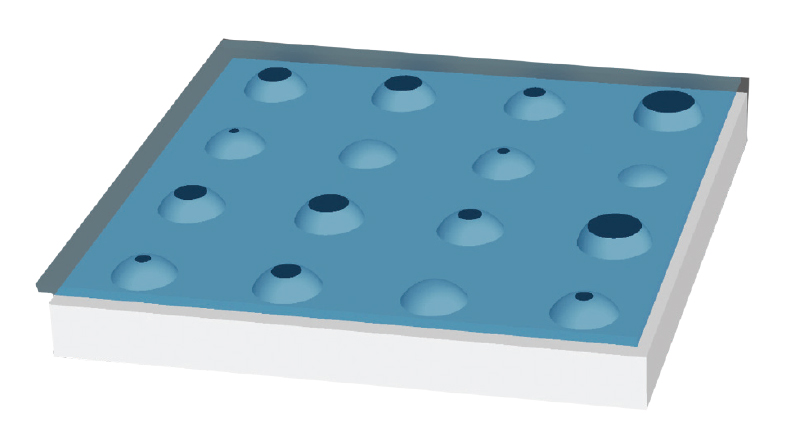
For this, the scientists used a surface thinly coated with graphene and demonstrated that it was possible to achieve superlubricity — that is, frictional forces were about a ten-thousandth of conventional friction. Such superlubricity is often associated (at a molecular level) with ultra-smooth surfaces such as graphene and has only been observed in labs where these surfaces are synthesised at nanometre or micron scales. If this can be achieved in machines and everyday mechanisms, it may be possible to reduce friction to negligible levels, which will lead to substantial energy savings and significantly diminished wear and tear. Notably, it is believed that almost 20% of global energy is used to overcome resistance caused by friction.
Greater friction control will help in the use of tactile interfaces that sense through contact and friction.
In a paper (bit.ly/486WiL5) published in the journal Physical Review Letters in January 2024, Brilliantov and colleagues, working in several research institutions, found that if the surface temperature of the interface was lowered, friction could be drastically reduced. This is because on highly smooth surfaces, friction is produced by synchronic fluctuations caused by random vibrations of surface atoms. They discovered that such vibrations existed at non-zero temperatures, and their intensity ebbed with decreasing temperatures.
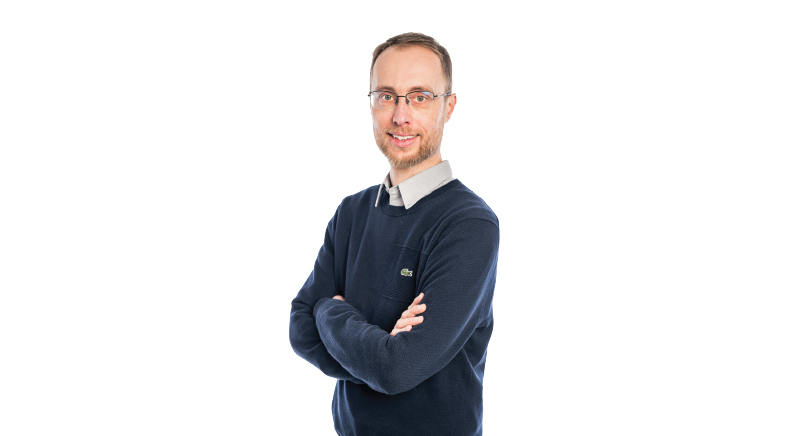
Brilliantov is hopeful that such a state of superlubricity will work in large-scale systems. "This is a matter of technological progress. One needs to create a molecular smooth surface at the macroscale, say, by covering (it) with a graphene layer. Current technology allows (us) to do this only on nano and micron scales," Brilliantov told IIT Madras Shaastra.
If friction can be removed in all working machines and mechanisms, the world will save an enormous amount of energy. "One can think about transport (trains, cars) sliding without friction and without complicated, bulky and expensive magnetic devices."
DUAL ROLE
Friction, of course, has its benefits. "We need friction. Without friction, cars won't move, pulleys won't work, and we may not be able to walk," says M.S. Bobji, Professor of Mechanical Engineering at IISc. Bobji, who has been studying different aspects of friction for years, points out that friction is used across the spectrum in everyday life. "So, we need to be careful where we want to reduce friction and where we want it to be higher," he says.
There are two types of friction: sliding friction and rolling friction. In a train, both are at play; the rail engine has sliding friction, while the bogies connected to it experience rolling friction. "For railroad and engines, the friction has to be high, while it should be low for the bogies," he says. Bobji adds that railways across the world have brought down the rolling friction for rail wagons to extremely low levels. The friction coefficient of most objects falls between 1 and 0, the former being the highest friction level. The friction coefficient of a railway wagon is around 0.005. Most machines use rolling friction as they have ball bearings lubricated with oil or grease.
Greater friction control will help in the use of tactile interfaces that sense through contact and friction, and reproduce interactive haptic feedback to moving fingers while operating robotic arms. It will be particularly useful in modern tools such as haptic devices and virtual reality gloves. It may, for instance, help a surgeon performing an endoscopic surgery match the pressure applied by fingertips with the force exerted by the tools performing the procedure inside the body. Right now, a lot of this depends on the skill and experience of the surgeon, Bobji points out.
A better grip over friction is the key to surmounting such challenges.
Have a
story idea?
Tell us.
Do you have a recent research paper or an idea for a science/technology-themed article that you'd like to tell us about?
GET IN TOUCH