A game-changing pharma innovation
-
- from Shaastra :: vol 02 issue 05 :: Sep - Oct 2023
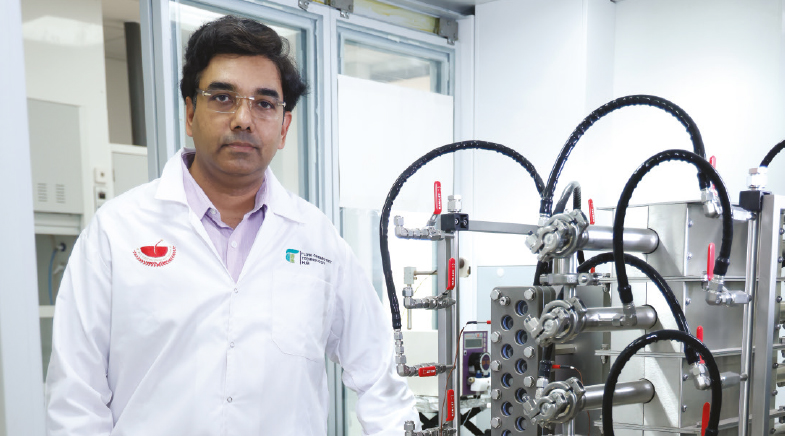
An advanced manufacturing technology promises a safer, faster and cheaper production of medicines. What does it entail?
Consider a conventional tablet-manufacturing factory. The ingredients are blended, granulated, compressed, and coated in discrete steps. Each of these needs its own 'clean room' with dedicated equipment and a low concentration of airborne particles. After each step, the material is stored, and samples are taken and tested in the laboratory for quality.
In the end, you get a 'batch' of tablets, lending the process its moniker 'batch manufacturing' — a process that is over 50 years old and used to make nearly all pharmaceuticals.
Such a factory covers a large geographical area, has extensive air-conditioning and ventilation systems, requires regular maintenance and employs plenty of labour, while frequent testing puts a "load" on the laboratory, says Mumbai-based drug industry consultant Kaushik Desai. Further, a batch, decided by the size of the equipment, takes months to produce.
But what if these operations were integrated into a connected and compact manufacturing system in a single room? Ingredients would enter at one end and tablets removed at the other. Quality would be monitored by Process Analytical Technology (PAT), sophisticated analytical tools using sensors and probes connected to the manufacturing line and software to analyse and manage data. One instance of a PAT tool is Near-Infrared Spectroscopy (NIR) — using near-infrared radiation to analyse the composition or characteristics of materials in real time.
The impact is potentially transformative. "Less area, fewer machines, less manpower," Desai says.
Now think of a Diwali firework like the 'flowerpot' or anaar. The risk of it exploding when lit does not deter the reveller. But what if the cracker were a hundred-fold larger, asks scientist Srinivas Oruganti. That, he says, would pose a "severe" problem. Manufacturers of a bulk drug — also called an active pharmaceutical ingredient (API), the key chemical that makes a medicine effective — routinely face this "inherent hazard" of certain chemical reactions.
In the bulk drug industry, unsafe chemistries become exponentially risky when the scale increases, as when they make their way from laboratory flasks into reactors of thousands of litres in the factory.
Take the toxic reactants cyanogen chloride and cyclopentadiene. These are used to make vince lactam, a building block for anti-HIV drugs abacavir and carbovir, and influenza drug peramivir. Contact with cyanogen chloride can severely burn the skin and eyes, while inhaling it can cause shortness of breath. Cyclopentadiene is flammable and thus a fire hazard.
There are instances of Indian producers importing unsafe chemistry, such as potentially hazardous Q-Acids, which are advanced intermediates to make the antibiotics levofloxacin and ofloxacin and are imported from China.
PAST ISSUES - Free to Read
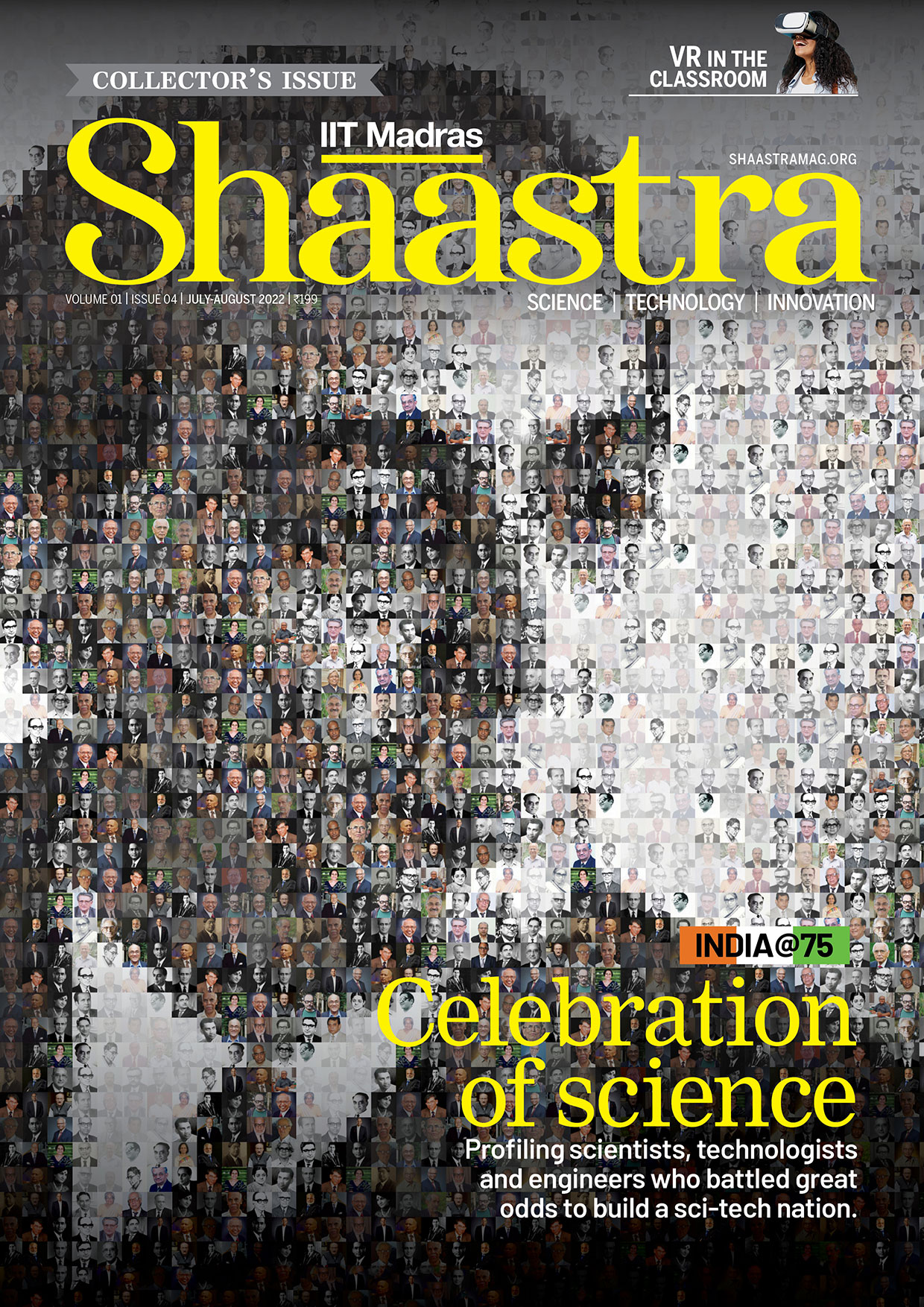
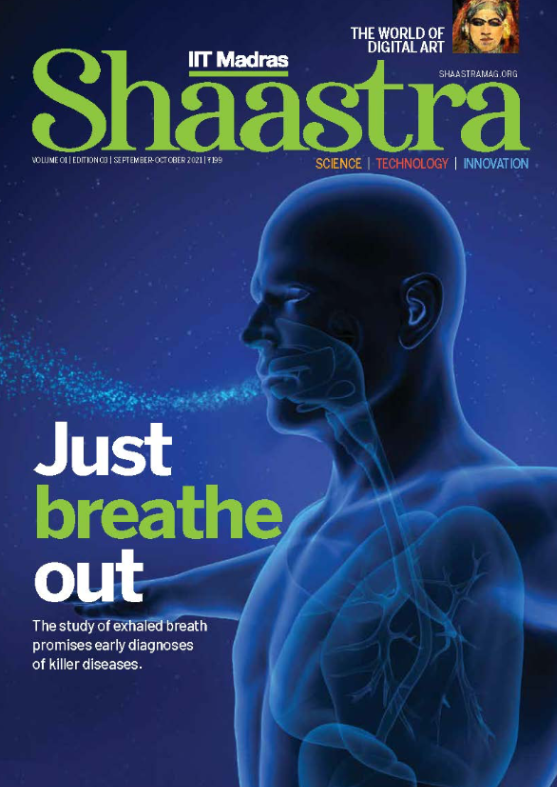
Have a
story idea?
Tell us.
Do you have a recent research paper or an idea for a science/technology-themed article that you'd like to tell us about?
GET IN TOUCH