Medtech mall
-
- from Shaastra :: vol 02 issue 06 :: Nov - Dec 2023
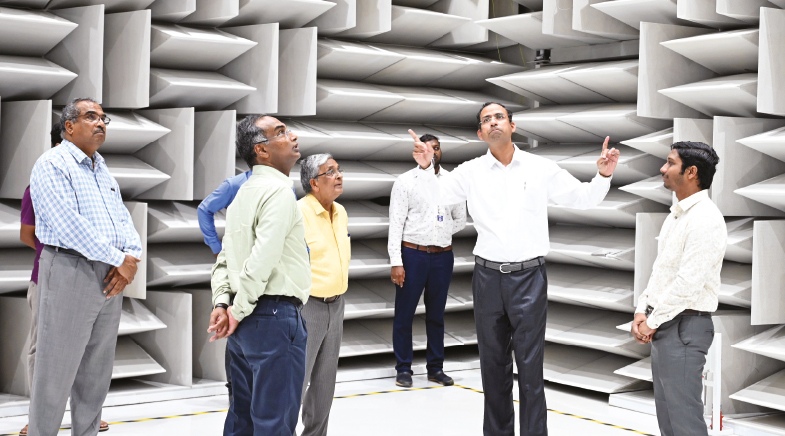
'Make in India' is the mantra of an ambitious manufacturing and innovation cluster.
An aviary is a wholly unexpected venue for a discussion on the serious business of medical technology. But that's the spot favoured by Jitendra Sharma, Managing Director and Founder-CEO of the Andhra Pradesh MedTech Zone (AMTZ). As budgerigars and lovebirds, with their insistent calls and showy colours, compete for attention with piped music, Sharma reflects on how the idea of a med tech park to spur domestic manufacturing took root and shape, in Visakhapatnam.
Like having an aviary on campus, little about this zone is par for the course. AMTZ came up over 270 acres of cleared forest land that, to begin with, did not have a cellular network or a PIN code. A solar farm and a convention centre are a few of the modern structures that stand over it now. Piped music plays across the campus as regulars and visitors shuttle between buildings along tree-lined roads in electric carts.
Set up five years ago, AMTZ is India's first integrated manufacturing and innovation cluster for medical devices. This, by itself, is noteworthy, as India imports most of its medical devices — from glucometers to Magnetic Resonance Imaging (MRI) machines. Equally remarkable is AMTZ's goal: to help achieve import neutrality by 2032 and for half the Indian hospitals to have half their equipment made in India by then. "That is what we see as our impact," Sharma says. "We are on track."
AMTZ currently has 133 companies on campus, making products ranging from printed circuit boards to superconducting magnets used in MRI, and 42 start-ups. An under-construction 200-bed hospital, when ready, will be proof that "an entire hospital can be operated using made-in-India devices", Sharma says. A university for med tech, to start enrolling by June 2024, will offer novel programmes in partnership with global universities.
Its secret sauce is the understanding that, in med tech, it is "science that drives business", Sharma says. "We are a science campus where business is the by-product; not an investment campus where science is the by-product."
The AMTZ experiment is being closely watched against the backdrop of the Indian government's policy and investment push to create manufacturing and innovation capacity in the medical technology sector. In the past, most industrial zones were presented as "real estate opportunities", says Rajiv Nath, advisor to AMTZ and Managing Director, Hindustan Syringes & Medical Devices (HMD), the maker of Dispo Van syringes. With discounted land as the draw, manufacturers then bought acres of it. And as most such zones lacked any other support, production was routinely deferred. Those attracted by tax holidays pulled out after the incentives ended, leaving ancillary producers in the lurch. But AMTZ, Nath stresses, is thriving and has emerged as a model for industrialisation, drawing visitors from other State governments planning their own parks.
A nascent AMTZ earned its spurs during the pandemic, when factories in the zone supplied 11 lakh of the 12 lakh COVID-19 testing kits required every day, Sharma says. They made personal protective gear, oxygen concentrators and ventilators, and AMTZ also produced its own equipment.
SHOPPING MALL FOR TECH
Sutures, thermometers, pacemakers or knee implants are all medical devices. So are operating theatre tables, and RT-PCR machines. This list translates into a diversity of inputs and technologies such as chemicals, textiles, electronics, radiation and 3D printing that go into their making. Testing is also complex. An MRI will be tested for electro-magnetic interference and noise levels, among other things. An implant will have to pass biocompatibility tests. Manufacturers aren't always sure what to test for and how. Testing services are often unavailable, and sending samples abroad is expensive and time-consuming.
AMTZ has 133 companies on campus, making products ranging from printed circuit boards to superconducting magnets used in MRIs.
AMTZ has identified and created a smorgasbord of common scientific and testing infrastructure on its campus. Many of these are being run in partnership with the private sector. The idea is to serve a spectrum of needs much like a "shopping mall", Sharma says.
For instance, a 3D-printing facility managed by private company THINK3D can print customised, high-precision and low-volume batch products such as skull implants and robotic surgical arms. Germany's safety and quality certification company TÜV Rheinland operates facilities that perform a battery of tests from acoustics and biomaterial checks to electro-magnetic compatibility. A gamma irradiation facility uses high-penetration energy rays that leave no residue and can thus sterilise products such as gloves and implants, where chemicals cannot be used.
This facility, along with an Indian Oil gas plant on the campus, was a big draw for Wadi Surgicals, says Selvam Subramaniam, Vice-President Operations. The company claims to run India's fastest production line for nitrile butadiene rubber gloves, capable of manufacturing a million pieces a day. The gas heats the processed water and curing oven used in production.
The facilities include a high-tech selective laser sintering machine used for printing with metal at the 3D printing centre. The TÜV-operated unit has a transmission electron microscope to study materials at an atomic level. "When the capabilities we needed were not in the zone, they (AMTZ) built them," says Chandrasekhar Nair, Chief Technology Officer at diagnostics company Molbio, an early mover into AMTZ. Molbio makes RT-PCR test cartridges and devices for COVID-19 and tuberculosis on campus.
An ancillary sector of key raw materials and components has also begun to emerge. Parts imported earlier are being manufactured at AMTZ. Among these are piezoelectric crystals needed in ultrasound machines; the superconducting magnet, which is the core component of an MRI machine; and the ultra-high-molecular-weight polyethylene (UHMWPE), a raw material used to make the liner between the metal joints of a knee implant. AMTZ also houses companies — such as the U.S.-based PCB assembly firm Amphenol — that serve a range of sectors including med tech.
OPEN TO ALL
AMTZ actively works in "finding gaps, travelling and identifying new companies and bringing them in", Molbio's Nair says. Consider the case of medical-grade UHMWPE. Its ability to resist wear and tear, among other qualities, makes it a good choice for orthopaedic implant liners. Implant-makers imported this plastic raw material but found supplies were expensive and scarce, says Abhishek Gupta, MD, Nanoshel Healthcare, which manufactures UHMWPE raw material in AMTZ and uses the co-located quality testing and irradiation facilities. AMTZ scouted Punjab-based UHMWPE maker Nanoshel, collaborated with it to upgrade UHMWPE to medical grade, and equipped a factory to make it using indigenised machinery. The company now caters to knee implant-makers in the country, and exports to Germany and the U.S. Local production has halved the cost of the raw material and ensured adequate supply, Gupta claims.
Factories in the zone supplied 11 lakh of the 12 lakh COVID-19 testing kits required every day.
The medical technology industry gets a boost when manufacturers that have capital and relevant knowhow in other sectors, such as Nanoshel, align themselves with the industry, Sharma points out. The Kalam Institute of Health Technology (KIHT), a health policy, research and technology institute supported by the Centre, provides producers with technology assistance, connecting innovators (such as academia) with industry, and provides market intelligence, among other things. KIHT, which Sharma calls the "brain" of AMTZ, is also behind recent government policies to boost local manufacturing.
Existing companies exploring new areas are here, too. Mumbai-based Accurex Biomedical, maker of biochemistry reagents and analysers, chose AMTZ to foray into point-of-care blood glucose testing devices. As it rented an AMTZ plug-and-play facility, it only incurred operating expenditure, Accurex MD Abhinav Thakur says. FoundryM, based in Medi Valley, one of the two incubators on campus (Bio Valley being the other), is contracted to develop a glucometer to Accurex's specifications. Finding such a company on the same campus is a "big plus", Thakur says. "Tech was the big deficit for us." The incubators are where the next generation of medical device companies is being nurtured.
One such outfit is Bengaluru-based Canmed Healthcare, which has designed an oral cooling system based on heat exchange, for head and neck cancer patients undergoing chemotherapy and radiation in hospitals. This could help prevent oral mucositis, a painful side-effect of treatment where ulcers form in the soft tissue of the oral cavity.
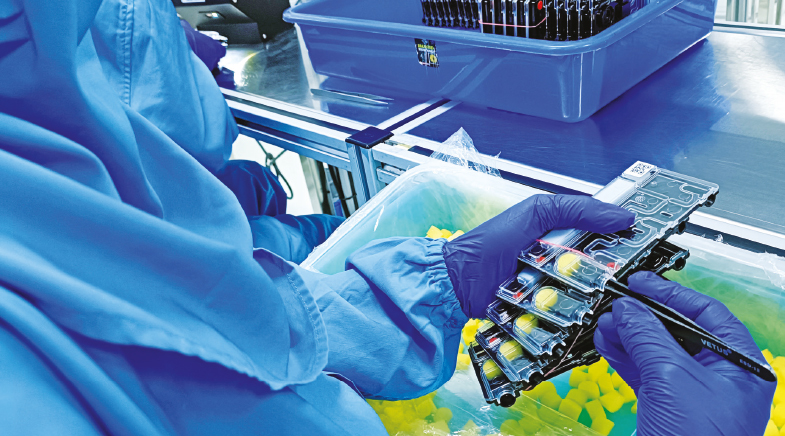
Ready with a prototype, Canmed Healthcare Managing Director Rama Krishnan was concerned about pre-approval testing. At Medi Valley, he gets to use the incubator's accredited pre-compliance laboratory at a nominal rate to test his product before it heads to the TÜV-run facilities for more expensive compliance-level testing and certification. When he wanted an aesthetically pleasing, medical-grade plastic panel for the equipment to replace serviceable metal, he turned to a fellow incubatee.
The incubatees that are yet to build their prototype can cost-effectively create multiple 3D-printed iterations at the Centre of Excellence (CoE) for Additive Manufacturing in AMTZ. The CoE also helps to identify and integrate the right components to improve performance, CEO Santosh Kumar Balivada says. Then, they can participate in workshops on subjects such as regulatory compliance and patenting held by the Indian Biomedical Skill Consortium (IBSC), another AMTZ initiative. Being located inside a med tech ecosystem means access to domain experts from among the manufacturers there, says Dilip Kumar Chekuri, CEO, AIC-AMTZ Medi Valley. For instance, the chief technical officer of a leading imaging company mentors radiology start-ups.
The upshot is that "the entire AMTZ ecosystem is integrated into (their) product development", says Susheela Branham, CEO of Bio Valley Incubation Council, which supports start-ups in life sciences and biotechnology that converge with med tech. It has clean rooms that can be used by biologics and in vitro testing companies, and houses a 3D bioprinting facility.
THE FUNDING SPIGOT
AMTZ has received funds from Central ministries and multilateral agencies. Capital equipment at the CoE for Additive Manufacturing, for instance, is funded by the Ministry of Electronics and Information Technology in line with a national policy for additive manufacturing. The incubators have Central government funding, too. Private companies are another source of funds. The hospital is a partnership with Australian firm Health 360°. Nath's HMD has supported AMTZ projects directly and through its corporate social responsibility foundation.
The zone still has some way to go; it will have to stand out over techno-industrial zones in other countries.
AMTZ, a private limited company of the Andhra Pradesh government, also earns revenue from sources such as testing facilities, prototyping, technology transfers and rentals. Its common facilities have attracted business from outside the campus, too — from med tech and others such as the Indian Navy (Visakhapatnam is the seat of the Eastern Naval Command), and from the consumer goods, ship-building, and space sectors.
THE ROAD AHEAD
The zone still has some way to go. To attract global companies, AMTZ will have to stand out over techno-industrial zones in countries such as Brazil, Malaysia and the Czech Republic. Quality expectations will have to be met in a country whose understaffed regulator is steering a rocky transition to med tech regulation. Companies making high-end medical devices should be "motivated and comfortable" to use AMTZ or a zone like it to manufacture in India, "for India and the world", says Milind Antani, who heads the med tech practice at Mumbai-based law firm Nishith Desai Associates. Policy and bureaucracy can smooth the way, but they will look to the zone for infrastructure, quality, technology, skilled human resources and to navigate the regulatory maze, he adds.
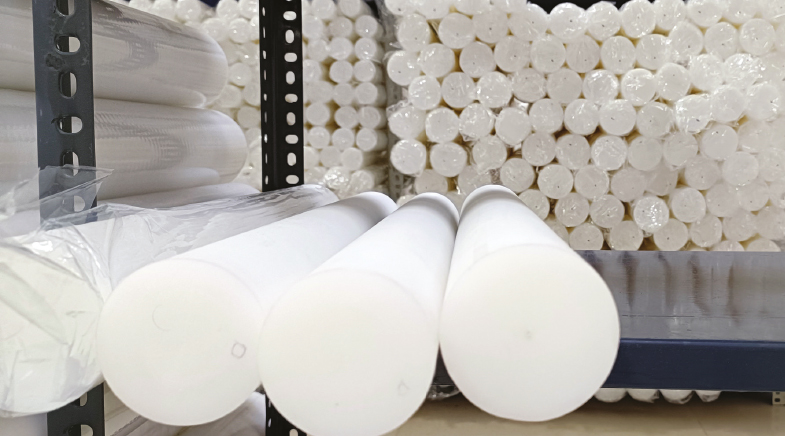
Sharma echoes some of these challenges but believes they can be mitigated. Investments in the common testing and scientific facilities in one place — more, he claims, than any other zone globally that caters to med tech — will continue to be its calling card. The upcoming university will pump out skilled biomedical engineers, med tech managers, and technologists from programmes designed by the IBSC, which already offers a range of certifications. The zone itself will evolve with technology, Sharma says.
"AMTZ will have to keep absorbing changes and creating a suitable value chain for the country," Sharma says. And by all accounts, he is the man to get the job done. His experience spans hospital administration to medical technology policy and advisory positions in India and multilateral agencies such as the World Health Organization. The need to boost manufacturing was brought home to Sharma and his team when he set up the division of healthcare technology in a Central government think tank. Under his supervision, the zone came up in in a record 342 days in 2018 on land allotted by the State government — Sharma was also advisor on health and med tech to the then Andhra Pradesh Chief Minister when the idea was conceived.
For a busy CEO, he is still "a WhatsApp message away", Nair holds. "He says, 'tell me what you want'," Accurex's Thakur adds. "'If you have an idea, I can help you bring it to life'."
Have a
story idea?
Tell us.
Do you have a recent research paper or an idea for a science/technology-themed article that you'd like to tell us about?
GET IN TOUCH