Perfecting alloys
-
- from Shaastra :: vol 03 issue 09 :: Oct 2024
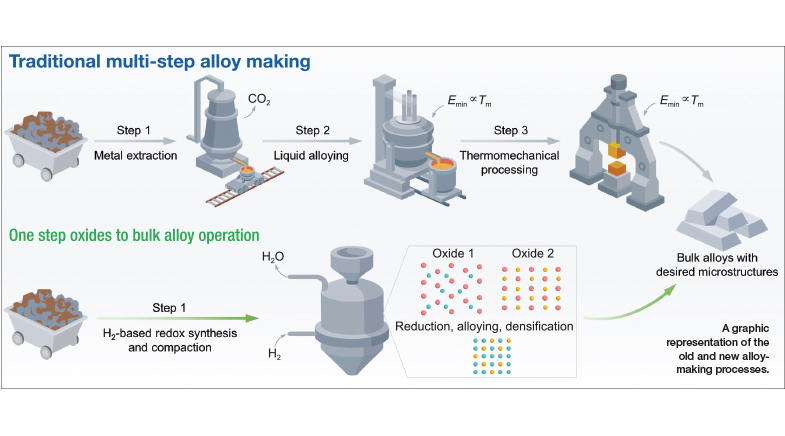
Scientists have developed a technology that turns
CO2-spewing metal oxides into green alloys.
Since the Bronze Age, the process of making alloys has more or less been the same. Now — after over 4,000 years — the old polluting method may be in for a makeover. Traditionally, metallurgical production followed a sequential approach of three key steps: reducing ores to their metallic form, mixing liquefied elements to create the alloy, and finally applying thermomechanical treatments to achieve the desired properties. Each step is energy-intensive and relies on carbon as both an energy carrier and a reducing agent, resulting in significant carbon dioxide (CO2) emissions. Conventional metallurgical processes account for about 10% of greenhouse gas emissions annually.
Now, in a proof-of-concept study, a team of researchers at the Max Planck Institute for Sustainable Materials (MPI SusMat), in Düsseldorf, Germany, has developed a single-step process that integrates metal extraction, alloying and thermomechanical processing. The team also demonstrated its feasibility by making a class of bulk alloys called nickel-iron invar alloys. These alloys with low coefficients of thermal expansion are widely used in aerospace, for making valves in engines, and precision instruments. It was discovered in 1895 by Charles Edouard Guillaume, and the finding won the Swiss physicist the 1920 Nobel Prize in Physics. The fabrication of it, however, is significantly polluting.
PAST ISSUES - Free to Read
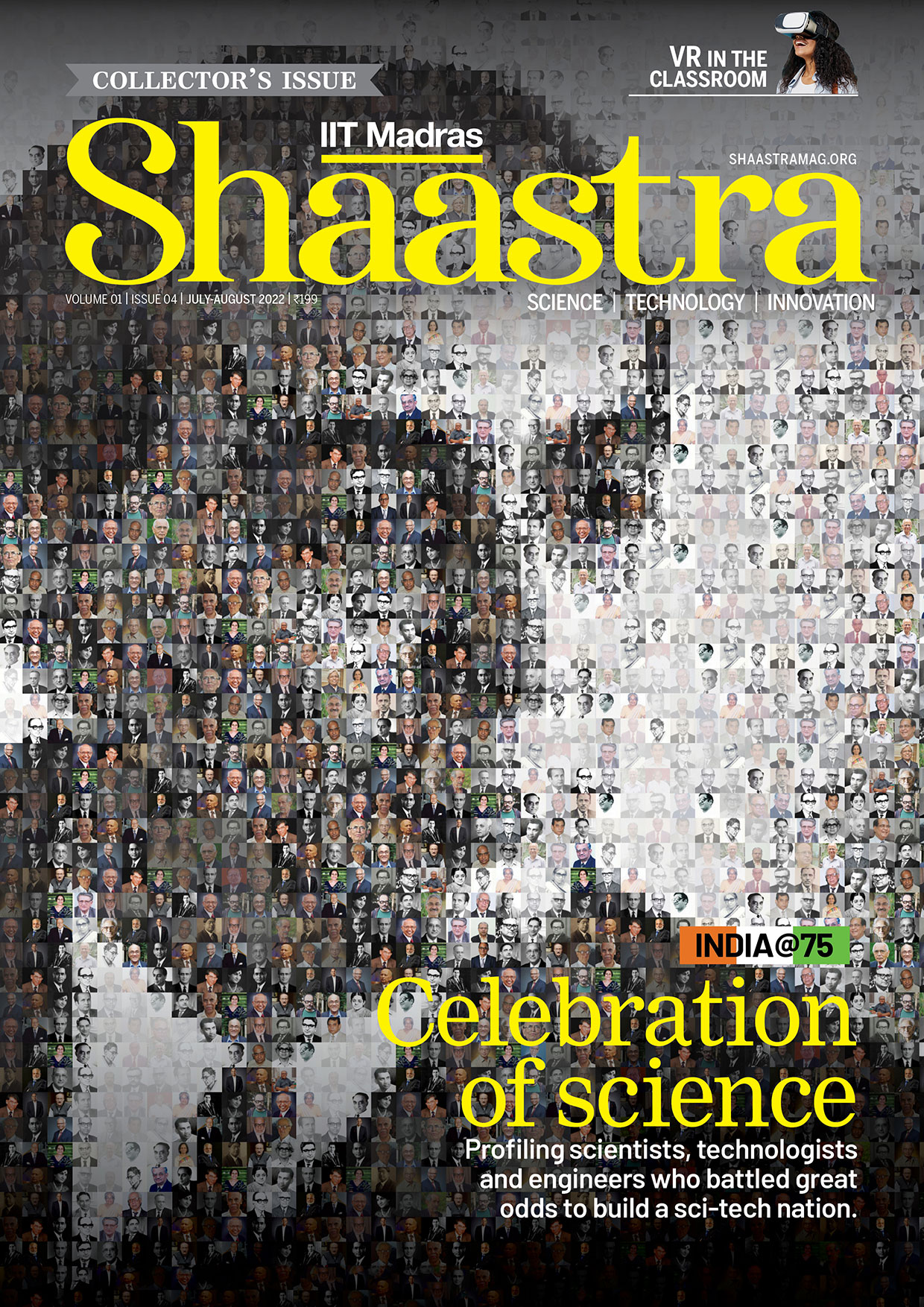
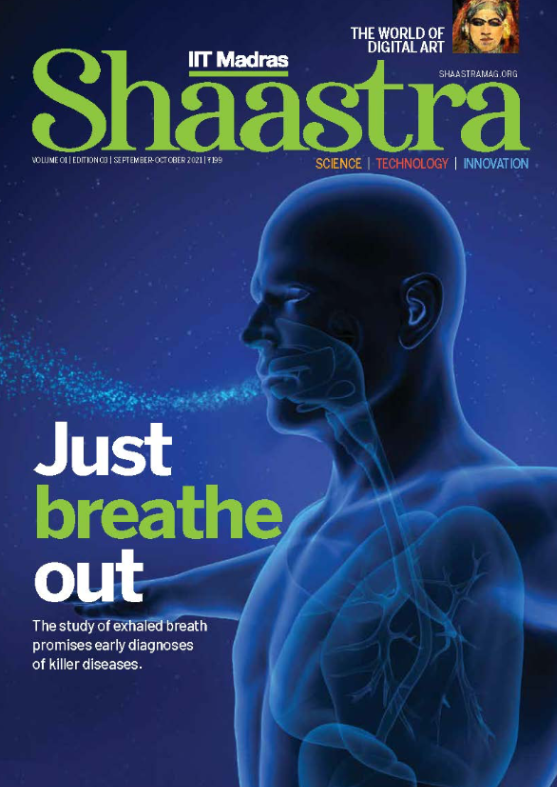
Have a
story idea?
Tell us.
Do you have a recent research paper or an idea for a science/technology-themed article that you'd like to tell us about?
GET IN TOUCH