E-fabrics of the future
-
- from Shaastra :: vol 03 issue 07 :: Aug 2024
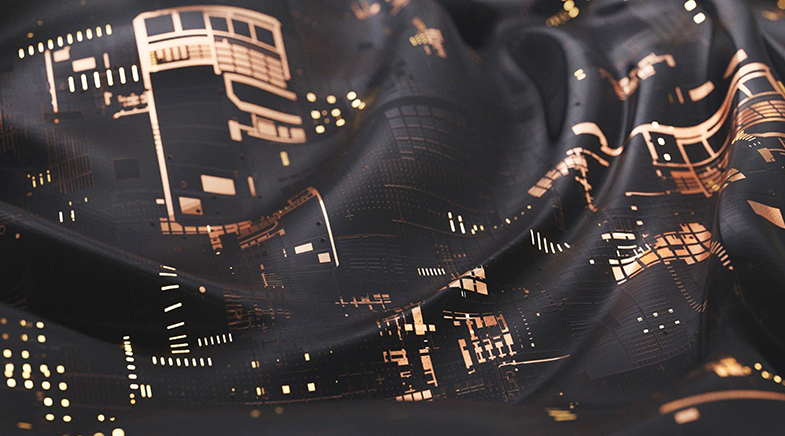
Advances in materials science allow electronic clothing that can monitor health continuously.
In 2016, Ajay Sangwan left his job as an industrial engineer to start his own venture in electronic textiles. During his final year of graduation from the National Institute of Fashion Technology, New Delhi, Sangwan had been involved in developing a prototype of a smart jacket for women – a safety jacket that senses an attack on the body via special sensors, gives an electric shock to the attacker and sends SOS alerts to family, friends and the police. The prototype, however, needed to be perfected. So, Sangwan partnered with engineers Vivek Jose and Rohit T., and incubated the start-up Nyokas Technologies in 2017 at Maker Village electronics incubator in Kochi. Later, another engineer Teny Thomas joined the team.
While the team was able to develop a working prototype of the self-protection jacket, it struggled to raise funding to scale it up. Smart textiles like these catered only to niche markets: their high costs meant they were not suited for a mass market. The team next took on the iDEX (Innovations for Defence Excellence) Challenge, an initiative of the Ministry of Defence, which asked for ideas to develop a smart jacket for the Indian Army. With their specialisation in electronic textiles, the team won the challenge and worked with the army to develop a modified bullet-proof jacket that also monitors body vitals such as heart rate, breathing rate, pulse and activity level, and sends this data along with location to the army unit. If a soldier is hit by a bullet, it also communicates information on the body part affected. All this data is transferred via radio frequency.
Textiles have been in use for 27,000 years but their utility has been confined to covering humans and objects.
What gives the smart jacket its functionality is a system of sensors laid over the vest area of the jacket via conductive ink. The system also contains a lightweight but rigid battery and a printed circuit board that needs to be kept in the pocket. The prototype is being tested by the army; if it is approved, it could be in use in six months. The Nyokas team wishes to incorporate yet more health-based sensors into the jacket to help track soldiers' performance during training and provide better assistance in case of an injury.
FITNESS TRACKERS
Various other companies and start-ups are also launching products for niche markets in healthcare, sports, military, fashion, comfort and transport. Canadian companies like Hexoskin, Myant and OMsignal and the U.S.-based Sensoria have developed smart shirts that monitor body vitals. The Japanese company Xenoma sells a smart shirt that tracks motion and posture, and can be used for fitness tracking, gaming and virtual reality applications. U.S.-based Athos produces smart fitness apparel that allows sportspersons to monitor their muscle exertion and optimise workouts. Sensoria's smart socks track foot pressure and gait to understand running form, foot-landing technique and balance, which can help prevent injuries and improve performance.
The Commuter Trucker Jacket developed by Google and Levi's allows wearers to interact with their smart devices through touch-sensitive areas on the jacket, allowing them to control music, receive notifications and access navigation. Indian start-up Broadcast Wearables created a touch-enabled, programmable, LED T-shirt that can display any slogan a user wants using their smartphone. According to a 2022 report by Allied Market Research, the market for e-textiles, valued at $367.2 million in 2021, is projected to grow to $721.8 million by 2031 (bit.ly/e-textile-market).
OPPOSITES UNITE
Textiles have been in use for 27,000 years, but only to cover humans and objects or as decoration. Parallelly, the electronics industry was also ripe for a rebranding. So it was natural for the two to fuse together. As Kaushik Parida, Assistant Professor at the Indian Institute of Technology Roorkee, points out, for the past 50 years, the driving factor for electronic devices has been miniaturisation. But that process may have run its course, under the influence of the quantum effect.
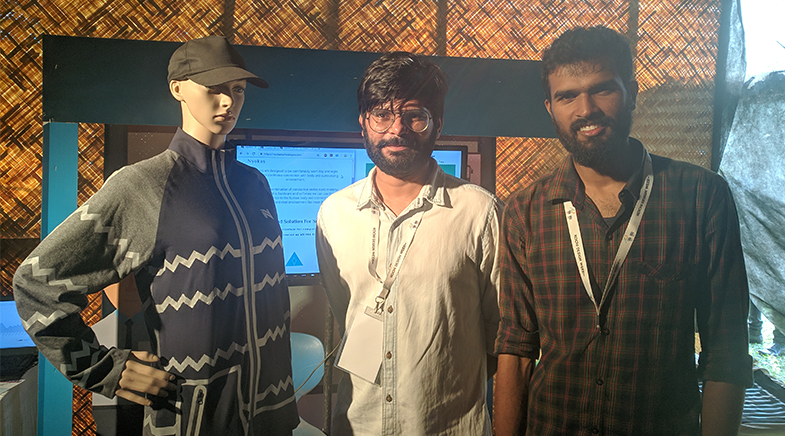
That 'marriage' of textiles and electronics is an unusual union. While electronics need power and are rigid, ubiquitous, connected, hydrophobic and smart (owing to processing power), textiles don't require power but need to be comfortable, flexible, breathable, washable and look smart. The union, however, was made possible by advances in materials science, which led to the development of conductive inks and yarns, progress in the field of miniaturisation of electronics, flexible and stretchable electronics, wireless communication, and encapsulation and coating techniques that protect electronics from water and detergents. Together, these technologies helped in the development of fabrics that are flexible, washable and durable, yet conductive.
CONDUCTING TEXTILES
Conductivity is the utmost requirement of e-textiles: it is the basis of the transmission of electric signals. There are two main approaches to making a textile conductive, explains Achu Chandran, Senior Scientist at CSIR-National Institute for Interdisciplinary Science and Technology (NIIST), Thiruvananthapuram. One way is to immerse the textile fibres into the conductive solutions and make each fibre conductive; the other is to print the circuit directly on to the substrate (textiles, in this case) using conductive ink. Printing the circuit is preferred as it allows for a more uniform and consistent conductive layer compared to conductive yarns; it also provides for a high degree of customisation in terms of pattern and area of conductivity, and precise application. It can easily be mass-produced through various printing platforms.
The 'marriage' of textiles and electronics is an unusual union that resulted in flexible, washable and conductive fabrics.
With a PhD in soft materials and devices, Chandran joined CSIR-NIIST in 2019. There he works with Surendran K.P., Principal Scientist, to develop better conductive inks for printing electronics on textiles and exploring their applications. A good conductive ink for printing electronics should be highly conductive, adhere well to textiles, and be flexible, stable, resistant to chemicals and cheap. It should have good printability and should dry or cure at normal room temperature conditions.
To make such an ink, the team successfully decorated silver nanoparticles of an average size of 12-13 nanometres on the surface of multi-walled carbon nanotubes. The unique selling point of the ink is its ability to cure at room temperature. The curing of ink increases its performance by improving its conductivity, adhesion to the substrate and resistance to environmental factors. The team uses a screen-printing methodology to print electronics onto textiles; it is like first developing a stencil based on circuit design and then using it to print the designed circuit on a fabric. In a research paper published in ACS Applied Materials & Interfaces (bit.ly/conductive-ink), the researchers showed various applications of such an ink. The ink was used to develop a smart glove that could flawlessly replicate the gestures of a human finger, a strain sensor that could sense even minute strains, a breath sensor that successfully identifies variations in human breath cycles, and an energy-efficient fabric heater suitable for wearable applications.
Chandran is interested in commercialising self-heating fabric with the potential to treat musculoskeletal injuries via thermotherapy. Such a lightweight heating fabric is better than conventionally used heat packs and wraps, which are heavy, bulky and mechanically rigid.
Materials advancement, miniaturisation and better printing technologies have advanced the frontiers of printed and flexible electronics in the past two decades. Better encapsulation and coating technologies have ensured that electronic components are protected from water, detergents and physical stress during washing.
The field of e-textiles has morphed from attaching electronics into the garment to embedding to integrating them. But although the electric circuits are now fully integrated with the textile, the batteries that power the circuits are still rigid, detachable and have to be carried around in a pocket. This makes the whole system bulky.
SELF-POWERED TEXTILES
Parida envisions a battery-less future for electronics. "In the future, we will have electronic devices which will generate energy from the ambient environment, store it and use it," he reckons. In electronic textiles, this will be particularly useful. Apart from the additional weight and rigidity, batteries have finite power, and charging them is a problem in remote areas.
Parida is working on creating clothing that can harvest energy on its own. To achieve this, his team has developed materials that use the principles of triboelectricity to generate current. The whole system, called a triboelectric nanogenerator, uses two layers of materials (fabric, rubber, and so on) that get charged when they rub against each other. When you move or push layers against each other, one layer gets positively charged and the other gets negatively charged. This charge difference creates a small electric current that can be used.
Parida's team created EVA/Nylon-11 micro/nano-fibres as the positive layer and EVA/PVDF/lead-free halide double perovskite micro/nano-fibres as the negative layer (bit.ly/energy-harvester). The team also checked the washability aspect of the fabric, and found that due to the water-repelling nature of its material, the performance remained intact even after four cycles of washing and drying. "We have developed a highly stretchable fabric that is also breathable in nature. And on a single tap, it can generate around 600 volts to power multiple small electronics devices," he adds.
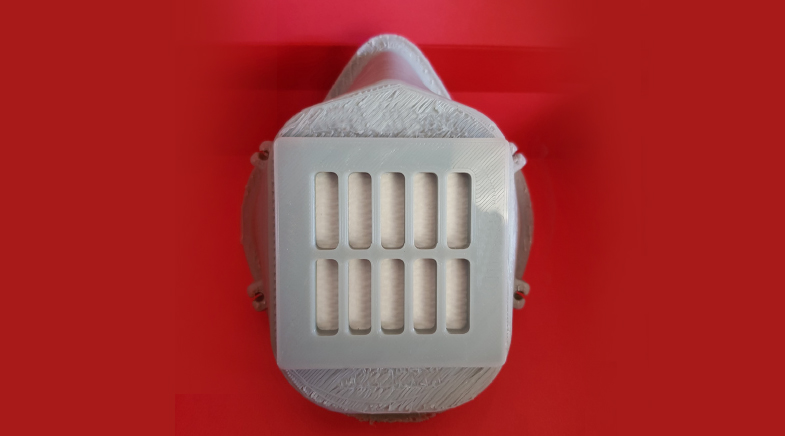
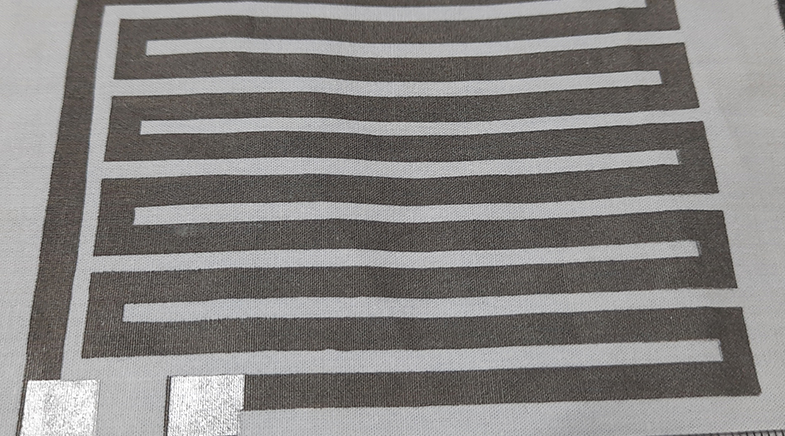
Researchers and companies across the world are using various forces of nature to generate self-powered textiles. Some are trying to harness energy from biomechanical motions like blood flow, breathing, and hand and leg movement by using the principles of electromagnetic, electrostatic, triboelectric and piezoelectric forces. Others are looking to harvest energy from body heat through thermoelectric generators that convert heat to electricity. Many start-ups and companies are also tapping sunlight by integrating printable solar cells on textiles. For example, U.S.-based Pvilion has developed flexible, lightweight solar panels that can be used in various applications, including clothing and tents. However, the game is all about enhancing the power that the systems can produce before commercialising them.
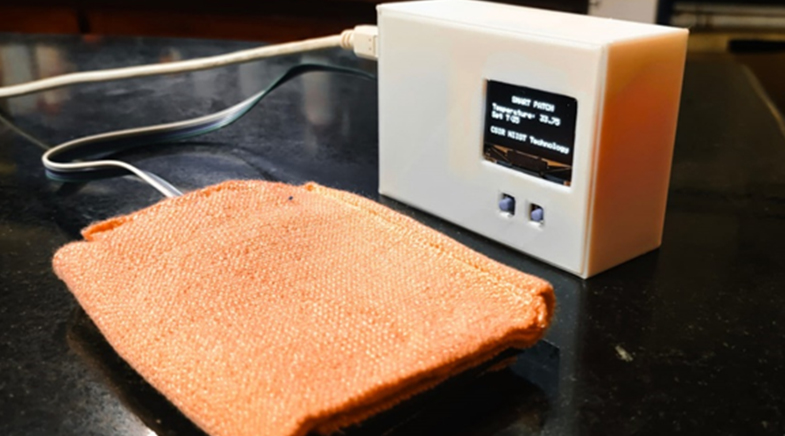
While wearable technology devices like smartwatches and bands have become quite popular in the past decade, especially to monitor body vitals, e-textiles do much more. Sangwan reckons that smartwatches are in any case not the gold standard for harvesting medical data from the wearer's body. "They are more lifestyle things," he adds. Besides, they monitor only a few body vitals, unlike e-garments, which cover the entire body area and offer continuous health monitoring and location detection. For example, Sandeep Arya's team at the University of Jammu has developed a human sweat-based wearable sensor on cotton fabric for real-time glucose monitoring (bit.ly/sweat-sensor).
Materials advancement, miniaturisation and better printing technologies have expanded the field of printed and flexible electronics.
Garments that cover the entire body provide an opportunity to monitor and treat various health conditions. As the technology matures, our bodies will become an interface to data, and our clothing will become an intelligent second skin.
Have a
story idea?
Tell us.
Do you have a recent research paper or an idea for a science/technology-themed article that you'd like to tell us about?
GET IN TOUCH